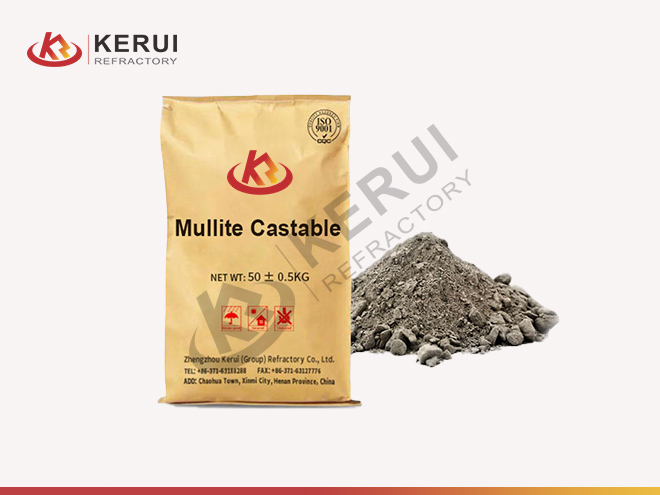
Mullite Refractory Castable
- Al2O3≥/%: 55-70
- Bulk Density≥/(g/cm³): 2.3-2.6
- Flexural Strength ≥/MPa: 7-9
- Max Service Temperature (℃): 1300-1500
- Permanent Linear Change ≤/%: ±0.5
- Certification: ISO9001/ISO14001/ISO45001/ISO50001
- Sample: testing of sample is available
Description of Mullite Refractory Castable
Mullite refractory castable is an unshaped refractory material composed of porous mullite aggregate, binder, and various additives. Mullite is a high-quality refractory raw material, and this type of mineral is relatively rare. The specific ingredient ratio can be adjusted according to the actual situation of the boiler. The refractoriness of mullite is 1790℃. Mullite castables are usually used in steelmaking, ceramics, petrochemical, and incineration industries. They can also be used as working linings in direct contact with flames, and have excellent heat insulation and heat resistance.
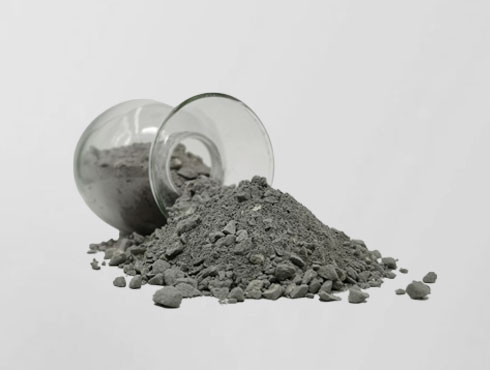
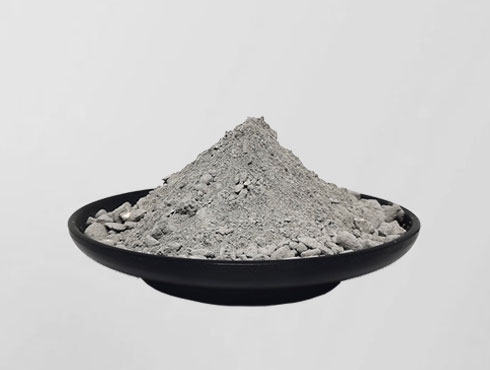
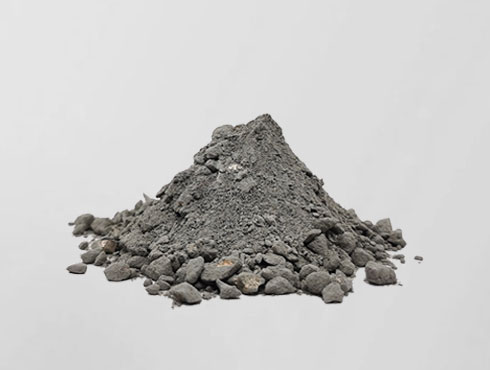
Kerui Mullite Refractory Castable Technical Data Sheet
Item/Grade | KRMJ-55 | KRMJ-60 | KRMJ-65 | KRMJ-70 |
---|---|---|---|---|
ω (Al2O3) ≥/% | 55 | 60 | 65 | 70 |
Bulk Density ≥/ (g/cm³) | 2.3 | 2.4 | 2.5 | 2.6 |
Flexural Strength ≥/MPa | 7 | 7 | 8 | 9 |
Compressive Strength ≥/MPa | 40 | 50 | 60 | 70 |
Permanent Linear Change ≤/% | ±0.5 | ±0.5 | ±0.5 | ±0.5 |
Advantages of Mullite Refractory Castable
Low Thermal Expansion
The low coefficient of thermal expansion of mullite castables means that they undergo minimal dimensional changes when heated. The property helps prevent cracking, and spalling and ensures the integrity and service life of the refractory lining.
Short Bake Time, No cracking
Mullite castables dry and cure quickly without visible cracking or damage. Their formulation and properties allow for shorter bake times than some other refractory materials, resulting in faster installation.
Environmental Friendly
Mullite castables usually do not contain harmful substances such as asbestos and other harmful substances, and during their production and application, it usually does not release a large number of harmful gases or particles into the environment.
Good Wear Resistance
Their composition and microstructure help them withstand attack by abrasive particles, making them suitable for applications exposed to abrasives, corrosive gases, or mechanical friction, reducing material loss and extending service life.
Manufacturing Process of Mullite Refractory Castable
Step 1
Accurately weigh mullite granules and fine powder according to the formula requirements. Static mixing for 5-10 minutes to ensure that the granules and fine powder are evenly mixed and a uniform particle size is obtained. At the same time, add admixtures such as water reducer and antiknock agent as needed.
Step 2
Put the mixed mullite raw materials into a small plastic bag. Seal the small plastic bags and place them in the bulk bag to protect the ingredients from moisture and other environmental elements. Proper storage and protection of the integrity of the raw material are critical to obtaining a high-quality mullite refractory castable.
Step 3
In the production process of mullite-based refractory castables, corundum particles are mainly used as the main component, and mullite powder is added as the densifying powder. This can effectively improve the load-bearing capacity, softness, peel resistance, and compressive strength of the product.
Application of Mullite Refractory Castable
Iron Industry
Mullite castables can be used in ladles, ladle linings in the steel industry, or tundishes in continuous casting systems. They have excellent thermal insulation properties and are resistant to the corrosive effects of molten metal and slag.
Petroleum Industry
Mullite castables are used for lining reactors, reformer tubes, flare stacks, furnaces, and other high-temperature equipment in petrochemical plants. Mullite castables have excellent thermal insulation and chemical resistance, making them suitable to withstand the harsh conditions encountered in the production of petrochemical products.
Glass Industry
The main applications of mullite in the glass industry are glass-melting furnaces, regenerators, port neck and throat areas, etc. They help to improve the heat exchange process and increase the overall energy efficiency of the glass manufacturing process.
Ceramic Industry
Mullite castables are widely used in the ceramic industry because of their excellent thermal stability, low thermal expansion, and chemical corrosion resistance. They are mainly used in kiln furniture, crucibles, saggers, drying Shelves, kiln car bases, etc.