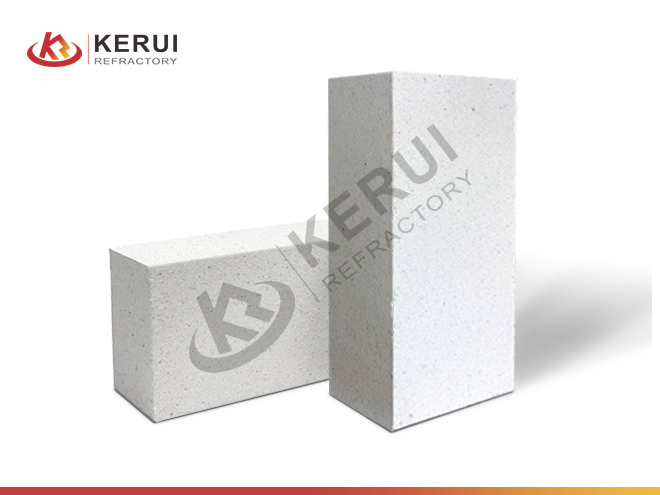
Silica Insulation Brick
- SiO2% (≥): 91
- Bulk Density (g/cm³): 1.0-1.2
- Refractoriness Under Load (℃)≥: 1400-1520
- Cold Crushing Strength (MPa)≥: 2.0-5.0
- Standard Size: 230*114*65mm
- Certification: ISO9001/ISO14001/ISO45001/ISO50001
- Sample: testing of sample is available
Description of Silica Insulation Brick
Silica insulation brick is also called lightweight silica brick, it is an insulation refractory material with a SiO2 of not less than 91%. Silica insulation brick is a kind of lightweight insulation material with excellent performance. Lightweight silica bricks use fine ore as raw material and add coke, wood chips, and other combustible substances to form a porous structure. The RUL of silicon insulation bricks is above 1620℃.
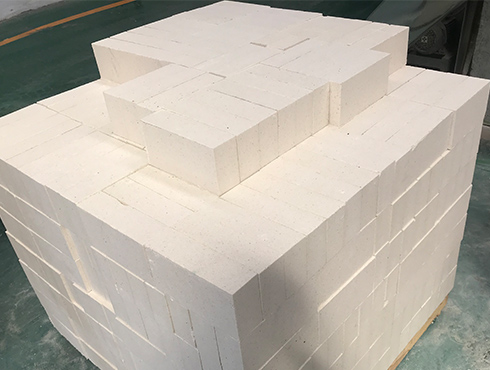
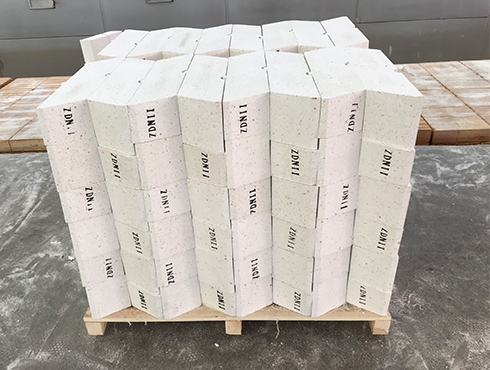
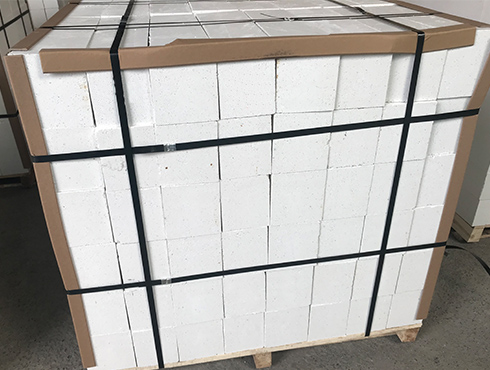
Kerui Silica Insulation Bricks Technical Data Sheet
Item/Grade | GGR-1.00 | GGR-1.10 | GGR-1.15 | GGR-1.20 | |
---|---|---|---|---|---|
ω (SiO2) ≥/% | 91 | 91 | 91 | 91 | |
Bulk Density ≥/(g/cm³) | 1.00 | 1.10 | 1.15 | 1.20 | |
Cold Crushing Strength ≥/MPa | 2.0 | 3.0 | 5.0 | 5.0 | |
Permanent Linear Change On Reheating ≤/℃ | 1500℃, 2h | / | / | 0.5 | 0.5 |
1450℃, 2h | 0.5 | 0.5 | / | / | |
0.1MPa Refractoriness Underload ≥/℃ | 1400 | 1420 | 1500 | 1520 | |
Thermal Conductivity Coefficient ≤/[W/(m·K)] (Average Temperature 350±10℃) | 0.55 | 0.60 | 0.65 | 0.70 |
Manufacturing Process of Silica Insulation Brick
Raw Material Preparation
Selecting silicon dioxide as the main component of the silica insulation brick, and adding a certain amount of auxiliary materials in addition to silica. Common auxiliary materials include refractory clay, refractory stone powder, calcination aids, heat stabilizers, etc. The crushed silica and auxiliary materials are mixed according to the formula ratio, and the mixed raw materials also need to be finely ground.
Grinding and Mixing
The grinding process needs to add an appropriate amount of wetting agent, which helps to improve the fluidity of the raw material and make the mixed raw material easy to shape. After grinding, the raw materials are monitored and analyzed to ensure that the particle size meets the requirements and to evaluate the uniformity and quality of the raw materials.
Forming
Forming is the process of shaping and pressing the mixed and ground brick material into the final brick shape. First of all, raw materials and molds should be prepared, and different molds should be selected according to the shape and size of silicon insulation bricks. Then the bricks are filled into the catty mold, and the bricks are evenly filled in by a mechanical device and then pressed into shape.
Drying
The drying process of silica insulation brick is the process of dehydrating the wet materials mixed in the upper part. The following is the description of the drying process:
Preliminary Drying:
The extruded bricks are dried in a well-ventilated area. At this stage, the water is fully evaporated.
Gradually Raise the Temperature:
After the initial drying, the silica insulation brick can be dried in a drying room. The purpose of gradually raising the temperature is to gradually remove the moisture inside the bricks, which will inevitably lead to the cracking of the bricks due to rapid temperature changes.
High-Temperature Drying:
On the basis of gradually increasing the temperature, further increase the temperature of the silicon insulation brick to between 500℃ and 1000℃. At high temperatures, the remaining moisture inside the brick will be evaporated, and the brick body will become dry.
Sintering
The sintering process is to calcinate the dry brick body at a temperature between 1300℃ and 1600℃. The purpose of this is to facilitate the chemical reaction and crystallization process. Isothermal usually takes several hours to ten hours. After the isothermal is over, just wait for the silicon insulation brick to drop to room temperature.
Cooling and Packaging
Cooling:
The calcined brick body is properly cooled. Place the fired weighing bricks in a well-ventilated area, and screen them after naturally cooling them to room temperature. The main reason is to see the appearance and quality of the bricks, and the precise size must meet the standards.
Packaging:
Pack the silicon insulation bricks that have passed the inspection and screening to protect the bricks from damage and pollution. Packing methods include. Packing method has the tray, high-quality plastic film, and the steel belt.
Advantages of Silica Insulation Bricks
Excellent Insulation Performance
Silicon insulation bricks have low thermal conductivity, which can effectively isolate the heat conduction between high temperature and low temperature, reduce energy loss and have excellent insulation performance. In a high temperature environment, silicon insulation bricks can maintain their good insulation properties and are not prone to heat leakage.
Good Thermal Shock Resistance
Silicon insulation bricks have good thermal shock resistance and can withstand severe temperature changes in high temperature environments without deformation and damage. This excellent performance can make the application of silicon insulation bricks for a long time.
Acid Corrosion Resistance
Because silicon insulation bricks are acidic, they can maintain their stability and integrity in strong acid environments. Its use can prevent corrosion and damage on the surface of the equipment and is widely used in acidic environments.
Environmental Friendly
Silicon insulation brick is an inorganic non-metallic raw material that does not contain harmful substances. Natural and harmless ores and materials are used, which can effectively reduce energy consumption and carbon dioxide emissions during the calcination process.
Application of Silica Insulation Bricks
The excellent performance of silica insulation bricks is widely used in metallurgy, electric power, glass, and other industries;
Metallurgical Industry
It can be used in smelting furnaces, smelting furnaces, rotary furnaces, heat shields, pipe insulation, pyrometallurgical electrolytic cells, smelting furnaces, etc.
Glass Industry
It can be used for glass melting furnaces, quenching furnaces, glass kilns, glass heat shields, etc.
Steel Industry
It also can be used in blast furnaces, ironmaking furnaces, converters, insulation layers, and heating furnaces of heat-insulated masonry.