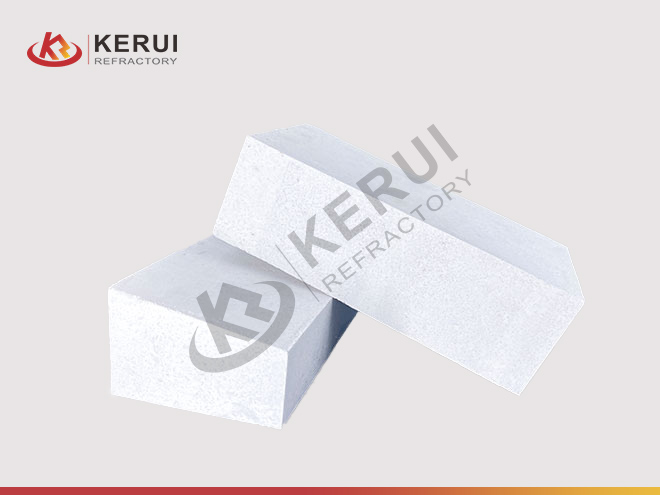
Corundum Brick
- Al2O3/%: 95-98
- SiO2/%: 0.15-0.5
- Fe2O3/%: 0.1-0.3
- Refractoriness Under Load: 1700MPa
- Cold crushing strength: 80-100MPa
- Certification: ISO9001/ISO14001/ISO45001/ISO50001
- Sample: testing of sample is available
Description of Corundum Brick
Corundum bricks are refractory products with corundum as the main crystal phase, in which the Al2O3 content is greater than 90%. High normal temperature compressive strength (up to 340MPa). High load softening start temperature (greater than 1700°C). Good chemical stability, strong resistance to acidic or alkaline slag, metal and glass liquid. The thermal shock stability is related to its structure, the corrosion resistance of dense products is good, but the thermal shock stability is poor. There are two types of sintered corundum bricks and fused corundum bricks. It can be made by using sintered alumina and fused corundum as raw materials, or bauxite clinker with high Al2O3/SiO2 ratio and sintered alumina, and is made by sintering method. Unfired corundum bricks can also be made with phosphoric acid or other binders.
Classification of Corundum Brick
Corundum Mullite Brick
Main material of corundum mullite brick is imported plate corundum, high pure fused corundum, adopt advanced superfine powder adding technology, it is made by the mixing material, drying, molding and burned in high temperature shuttle kiln.
Fused Corundum Brick
Fused corundum bricks are made by melting alumina in an electric arc furnace and casting it into a specified model of a specific shape. The desired product is obtained by annealing and holding, and then by processing with diamond abrasives.
Chrome Corundum Brick
Chrome corundum brick is also called high wear-resistant chrome corundum tapping brick. Using α-Al2O3 as raw material, appropriate amount of chromia powder and chrome corundum clinker fine powder are added, and then they are shaped and burned at high temperature. The main mineral composition is α-Al2O3-Cr2O3 solid solution. Minor minerals consist of a small amount of composite spinel (or no composite spinel), refractory bricks with 1% to 30% chromium oxide content.
GET PRICE
High Chromium Brick
High chromium bricks are made of chromium oxide and alumina as the main raw materials, or a small amount of zirconium oxide is introduced. After high temperature firing into. The content of chromium oxide is not less than 75%, and the content of chromium oxide and alumina is not less than 98% of the shaped refractory products. High chromium bricks have excellent resistance to leaching, high compressive strength at room temperature, excellent wear resistance, high temperature resistance, good thermal shock resistance, etc.
GET PRICE
Kerui Corundum Brick Technical Data Sheet
Item/Grade | GYZ-99A | GYZ-99B | GYZ-98 | GYZ-95 | |
---|---|---|---|---|---|
ω (Al2O3)/% | μ0 ≥ | 99.0 | 99.0 | 98.0 | 95.0 |
ở | 0.30 | ||||
ω (SiO2)/% | μ0 ≤ | 0.15 | 0.2 | 0.5 | / |
ở | 0.08 | ||||
ω (Fe2O3)/% | μ0 ≤ | 0.10 | 0.15 | 0.2 | 0.3 |
ở | 0.03 | ||||
Apparent Porosity/% | μ0 ≤ | 19 | 19 | 19 | 20 |
ở | 1 | ||||
Bulk Density (g/cm³) | μ0 ≤ | 3.20 | 3.15 | 3.15 | 3.1 |
ở | 0.05 | ||||
Cold Crushing Strength/MPa | μ0 ≥ | 80 | 80 | 80 | 100 |
ở | 15 | ||||
Permanent Linear Change (1600℃*3h)/% | Xmin Xmax |
-0.2~+0.2 | -0.2~+0.2 | -0.2~+0.2 | -0.3~+0.3 |
0.2MPa 0.6% Refractoriness Underload/℃ | Xmin | 1700 | 1700 | 1700 | 1700 |
Advantages of Corundum Brick
High Hardness
Corundum brick has a very high hardness, the hardness of corundum brick is close to Mohs hardness 9, which is harder than steel.
Corrosion Resistance
Corundum bricks have high corrosion resistance to various acids, alkalis and chemical solutions, and can work stably in harsh chemical environments.
High Temperature Resistance
The load softening degree of corundum bricks is generally between 1600-1800 degrees, and its refractory temperature can reach between 1770-2000 degrees.
Dimensional Stability
Corundum bricks have good thermal shock resistance, and the refractoriness is not lower than 1690 degrees. Its linear expansion coefficient between 20-450 degrees is about 0.03mm/degree, so it can withstand high temperature melt flow static pressure without rupture.
Excellent Insulation Performance
Corundum brick is an excellent insulation material, which can block current and heat conduction, and is suitable for high temperature electrical insulation and heat insulation applications.
Good Air Permeability
the gas precipitated in the zirconium corundum brick melt can penetrate out from the gaps of the silica sand particles in the molding wall, so the air permeability is good.
Application of Corundum Brick
Used in iron-making blast furnaces and hot blast furnaces, steel-making furnace external refining furnaces, sliding water heaters, glass melting furnaces and petrochemical industrial furnaces.