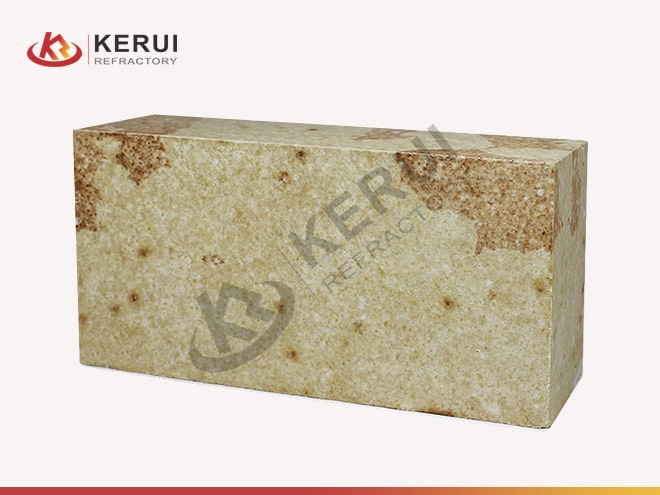
Silica Fire Brick
Mainly used as structural materials for coke ovens, glass furnaces, acid steelmaking furnaces and other thermal equipment.
- SiO2%: ≥94
- Fe2O3/%: ≤1.4
- True Density (g/cm³): ≤2.35
- Refractoriness Under Load (℃): ≥1650
- Standard Size: 230*114*65mm
- Certification: ISO9001/ISO14001/ISO45001/ISO50001
- Sample: testing of sample is available
Description of Silica Fire Brick
Refractory silica brick is an acid refractory material mainly composed of tridymite, cristobalite and a small amount of residual quartz and glass phase. The silica content is above 94%. The true density is 2.35g/cm3. It has anti-acid slag corrosion performance. Higher high temperature strength. The temperature of softening under load is 1620~1670℃. Long-term use at high temperature without deformation. Low thermal shock stability (heat exchange in water is 1~4 times). Natural silica is used as raw material, and an appropriate amount of mineralizer is added to promote the conversion of quartz in the green body to tridymite. Slowly fired at 1350-1430°C under reducing atmosphere. When heated to 1450°C, there will be about 1.5~2.2% of the total volume expansion, and this residual expansion will make the cuts close together, ensuring good air tightness and structural strength of the masonry.
Please Note: In addition to silica refractory bricks, we also offer silica insulation brick.
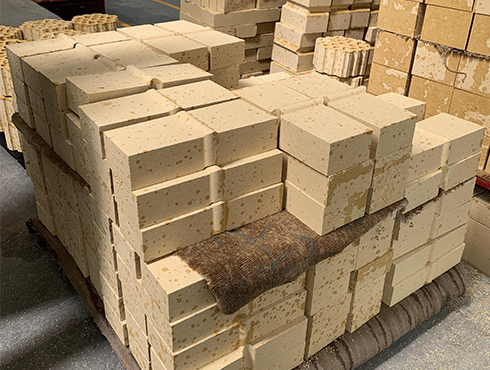
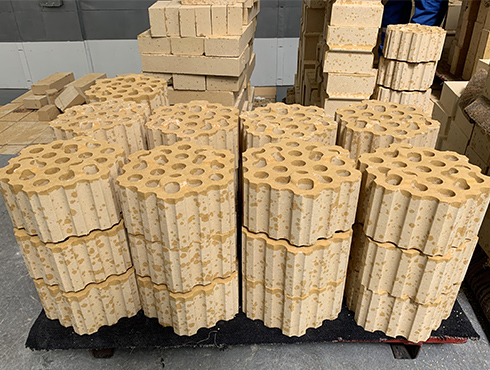
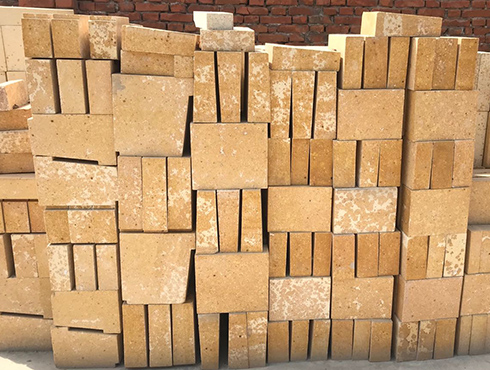
KERUI Silica Fire Brick Technique Data Sheet
Item/Grade | GZ-94 | |
---|---|---|
ω (SiO2)/% | μ0 | ≥94 |
σ | 1.0 | |
ω (Fe2O3)/% | μ0 | ≤1.4 |
σ | 0.3 | |
Apparent Porosity/% | μ0 | ≤24 |
σ | 1.5 | |
True Density (g/cm³) | μ0 | ≤2.35 |
σ | 0.1 | |
Cold Crushing Strength/MPa | μ0 | ≥30 |
σ | 10 | |
Xmin | 20 | |
0.2MPa Refractoriness Underload/℃ | μ0 | ≥1650 |
σ | 13 |
Advantages of Silica Fire Brick
High Temperature Resistance
The refractoriness of silica bricks is 1690℃ to 1730℃. It can maintain the stability and integrity of the structure at high temperature.
Excellent Thermal Conductivity
Refractory silica bricks have good thermal conductivity, and the load softening temperature is high, generally above 1620℃, which is only 70-80℃ lower than its refractoriness. The thermal conductivity of silica bricks increases with increasing operating temperature without residual shrinkage.
Excellent Corrosion Resistance
Silica brick is an acid refractory material, which has good resistance to acid slag erosion, and has high corrosion resistance to acids, alkalis, solution and other chemical substances.
Dimensional Stability
Refractory silica bricks have a low thermal expansion coefficient, so the dimensional change is small under high temperature environment.
Customizability
Refractory silica bricks can be customized according to different needs, including size, shape and refractory grade.
Application of Silica Fire Brick
Metallurgical Industry
Refractory silica bricks are widely used in high-temperature smelting equipment such as blast furnaces, steelmaking furnaces, ironmaking furnaces, electric furnaces and molten iron treatment equipment in the metallurgical industry.
Chemical Industry
Refractory silica bricks are used in high temperature reaction furnaces, kilns, reforming furnaces, heating furnaces, heat exchangers and grates in the chemical industry.
Electric Power Industry
Refractory silica bricks are widely used in the electric power industry for high-temperature equipment such as combustion furnaces, boilers, chimneys, and thermal power stations.
Glass and Ceramic Industry
Refractory silica bricks are used in glass and ceramic industries for equipment such as glass melting furnaces, kilns and kiln furniture. Because of their high heat resistance, they can withstand the melting process of high-temperature glass and ceramic materials, ensuring product quality and production efficiency.
Iron and Steel Industry
Refractory silica bricks are widely used in the iron and steel industry for equipment such as ladles, iron gates, sprue and molten iron wells. They can withstand the impact and corrosion of high-temperature molten steel, protecting the durability and production efficiency of equipment.