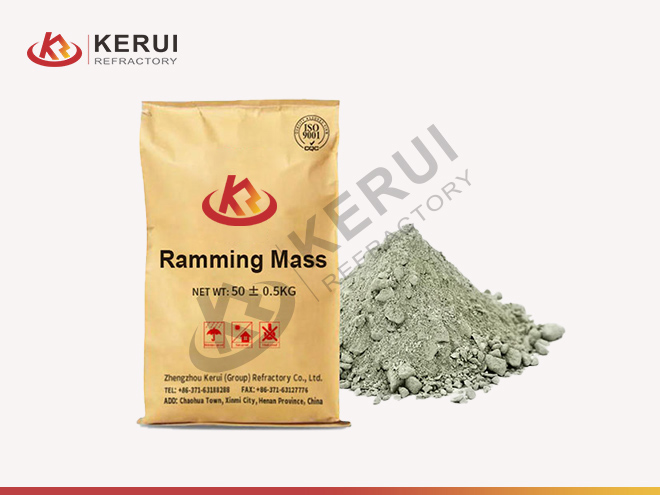
Ramming Mass
- Acidic ramming mass
- Neutral ramming mass
- Basic ramming mass
- Certification: ISO9001/ISO14001/ISO45001/ISO50001
- Sample: testing of sample is available
Description of Ramming Mass
Ramming mass is a refractory material made by ramming process. It is composed of various aggregates, binders and additives. We supply different types of ramming mass, including acidic ramming mass, neutral ramming mass and basic ramming mass, as follows:
KERUI Acidic ramming mass: silica ramming mass and quartz ramming mass, etc.;
KERUI Neutral ramming mass: corundum ramming mass, mullite ramming mass and aluminum ramming mass, etc.;
KERUI Basic ramming mass: magnesia ramming mass, magnesia aluminum ramming mass and aluminum magnesia ramming mass, etc.;
The ramming mass on this website are only part of our supply. If you need other types of ramming materials, please contact us and our engineers will provide you with professional services!
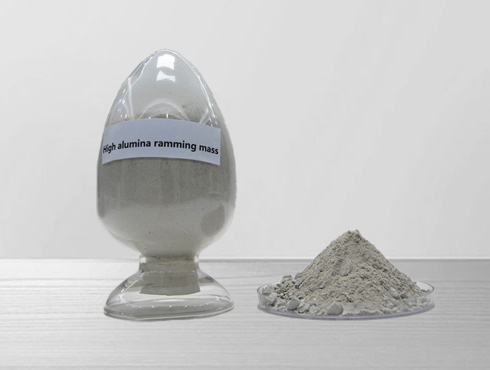
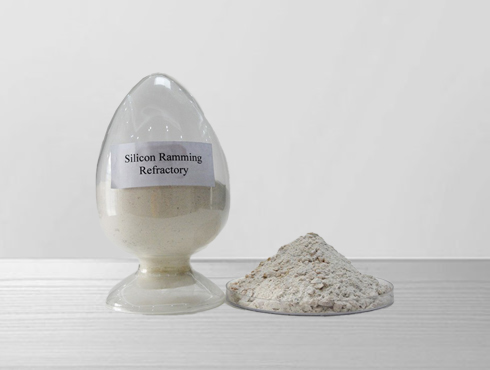
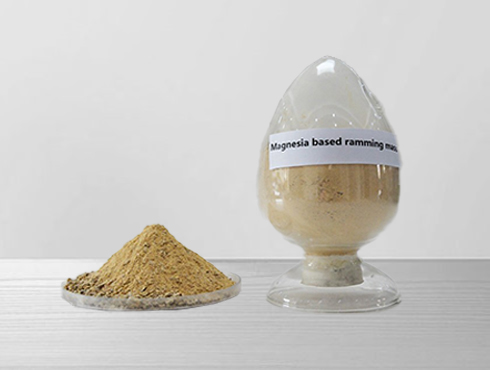
Kerui Ramming Mass Technical Data Sheet
Item/Grade | Neutral Ramming Mass | Acidic Ramming Mass | Basic Ramming Mass | ||||||
---|---|---|---|---|---|---|---|---|---|
Corundum Ramming Mass | Mullite Ramming Mass | Alumina Ramming Mass | Silica Ramming Mass | Quartz Ramming Mass | Dolomite Ramming Mix | Magnesia Ramming Mass | Alumina Magnesia Spinel Ramming Mass | Magnesia-Alumina Spinel Ramming Mass | |
ω (MgO)/% | / | / | / | / | / | 30-40 | ≥96 | 11-32 | 75 |
ω (Al2O3)/% | 90 | >80 | 45-90 | 0.8 | / | / | <1.5 | 65-88 | 22 |
ω (CaO)/% | / | / | 2 | / | / | 40-60 | / | 1 | / |
ω (SiO2)/% | / | <16 | 45663 | 98 | 98.5 | / | <2 | 1 | / |
Bulk Density (g/cm³) | 2.95-3.15 | 2.6 | 2.3-2.7 | 1.9-2.2 | 2.1-2.3 | 2.8-3.2 | 2.85-2.9 | 2.95-3.15 | 3.05 |
Max Working Temperature/℃ | 1800 | 1400 | 1400-1700 | 1650 | 1600-1750 | 1580-1900 | 1800 | 1800 | 1800 |
Advantages of Ramming Mass
Excellent Thermal Shock Resistance
Ramming mass has good thermal shock resistance and can withstand thermal shock impact caused by rapid temperature changes. It resists thermal stresses generated by temperature gradients to avoid cracking or breaking. This property makes the ramming mass suitable for processes that experience frequent temperature changes and provides reliable protection.
High Strength and Wear Resistance
Ramming mass has high strength and abrasion resistance to withstand mechanical stress and wear inside the equipment. It maintains the integrity and stability of the liner, extending the life of the equipment. This high strength and wear resistance allows the ramming mass to maintain the integrity and stability of the liner, reducing the frequency of repairs and replacements and saving maintenance costs.
Good Chemical Resistance
Ramming mass is resistant to acids, alkalis, and other corrosive media. It protects the interior of the equipment from chemicals and maintains the integrity and performance of the lining. This chemical resistance makes ramming mass an important material for chemical, metallurgical, and other related industries.
Low Coefficient of Thermal Expansion
The coefficient of thermal expansion is the rate of change in the length or volume of a material as the temperature changes. The ramming mass have a low coefficient of thermal expansion, meaning that they expand relatively little at high temperatures. It reduces the risk of damage caused by thermal stress and thermal shock and improves the stability and durability of the liner.
Application of Ramming Mass
Kiln Lining
Ramming mass is most commonly used for lining various types of kilns, such as lime kilns, cement kilns, ceramic kilns, etc. It provides excellent refractory properties and thermal isolation to withstand high temperatures and chemical attacks, protecting the kiln structure from damage.
Thermal Power Industry
Ramming mass also have important applications in the power generation industry, primarily in the lining and maintenance of boilers, combustion systems, chimneys and flues, and burner repair. The application of ramming mass in dynamic power generation maintains the stability and integrity of the hot stove structure, reduces heat loss, and reduces wear and corrosion of the equipment.
Cement Industry
The main applications of ramming mass in the cement industry are the lining of cement kilns and rotary kilns, kiln heads and tails, and the repair of kiln walls. The various kiln interiors in the cement industry are exposed to extreme environments of high temperatures and chemical attack, and refractory pounding compounds are able to withstand these challenges by providing refractory properties and chemical attack resistance to ensure the protection and stable operation of the kiln interior.
Steel Industry
The main applications of ramming mass in the steel industry are converter lining, electric arc furnace lining, ladle lining, hot blast furnace lining, etc. Various high-temperature furnaces in the steel industry are subjected to high temperatures and chemical attacks. The application of refractory batter not only provides refractory properties and chemical resistance, but also protects the ladle from erosion and penetration of high-temperature steel, and provides thermal isolation to keep the steel temperature stable.