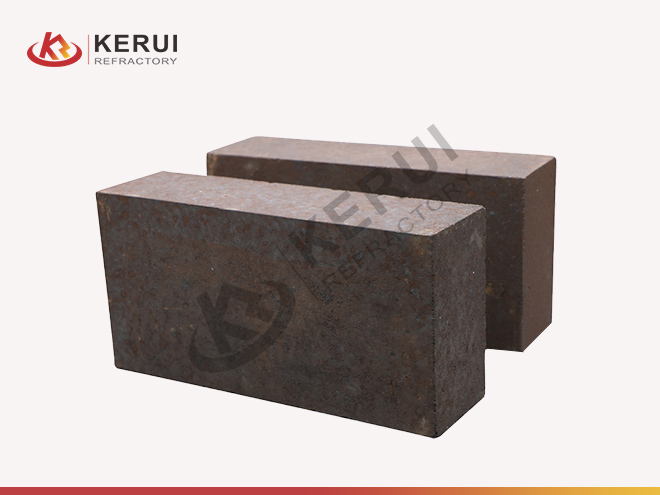
Magnesia Chrome Brick
Mainly in metallurgical industry, such as constructing open-hearth furnace tops, electric furnace tops, external refining furnaces and various alkali-resistant non-ferrous metal smelting furnaces.
- MgO%(≥): 45-65
- Cr2O3%(≥): 8-16
- Apparent Porosity/%(≤): 19-21
- Cold Crushing Strength (MPa): 20-35
- Standard Size: 230*114*65mm
- Sample: testing of sample is available
Description of Magnesia Chrome Brick
Magnesia-chrome bricks are refractory products with magnesium oxide (MgO) and chromium oxide (Cr2O3) as the main components, and periclase and spinel as the main mineral components. Generally, those with chrome ore added less than 50% are called magnesia-chrome bricks, and those with more than or equal to 50% are called chrome-magnesia bricks.
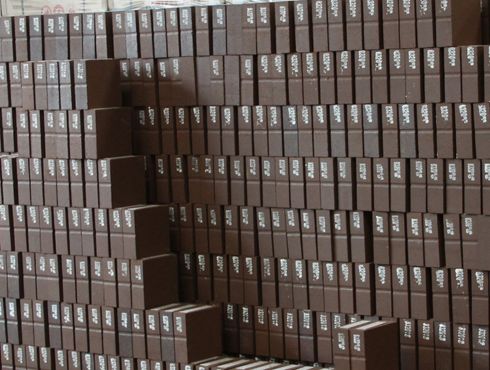
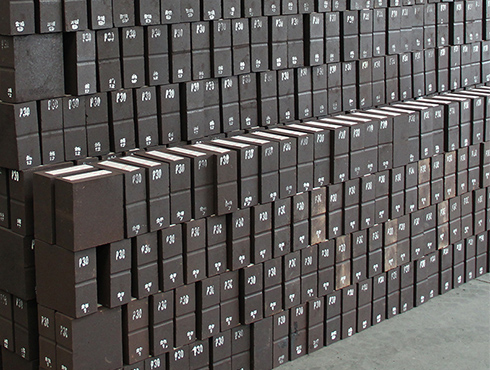
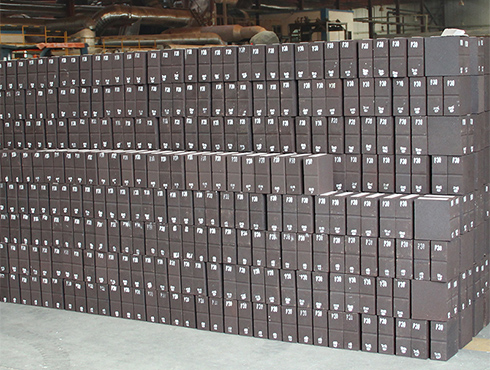
Kerui Magnesia Chrome Brick Technical Data Sheet
Item/Grade | MGe-16A | MGe-16B | MGe-12A | MGe-12B | MGe-8A | MGe-8B | |
---|---|---|---|---|---|---|---|
ω (MgO)/% | μ0 ≥ | 50 | 45 | 60 | 55 | 65 | 60 |
ở | 2.5 | ||||||
ω (Cr2O3)/% | μ0 ≥ | 16 | 16 | 12 | 12 | 8 | 8 |
ở | 1.5 | ||||||
Apparent Porosity/% | μ0 ≤ | 19 | 22 | 19 | 21 | 19 | 21 |
ở | 1.5 | ||||||
Cold Crushing Strength/MPa | μ0 ≥ | 35 | 25 | 35 | 30 | 35 | 30 |
Xmin | 30 | 20 | 30 | 25 | 30 | 25 | |
ở | 15 | ||||||
0.2MPa Refractoriness Underload T0.6/℃ | μ0 ≥ | 1650 | 1550 | 1650 | 1550 | 1650 | 1530 |
ở | 20 |
Tips
MGe6/MGe8/MGe12/MGe16=Commom Magnesia Chrome Brick
DMGe6/DMGe8/DMGe12/DMGe16=Direct-Bonded Magnesia Chrome Brick
Model | SRMGe16 | SRMGe18 | SRMGe20 | SRMGe22 | SRMGe26 | RMG0e12 | RMGe14 |
---|---|---|---|---|---|---|---|
MgO % | 68 | 64 | 65 | 56 | 56 | 75 | 75 |
Cr2O3 % | 16 | 18 | 20 | 22 | 26 | 12 | 14 |
SiO2 % | 1.5 | 1.5 | 1 | 2.5 | 2.5 | 1.5 | 1.5 |
Apparent Porosity % | 16 | 16 | 14 | 16 | 16 | 15 | 15 |
Bulk Density g/cm3 | 3.1 | 3.1 | 3.1 | 3.1 | 3.1 | 3.2 | 3.2 |
Cold Crushing Strength Mpa | 40 | 40 | 40 | 40 | 40 | 50 | 50 |
Refractoriness Under Load °C | 1700 | 1700 | 1700 | 1700 | 1700 | 1700 | 1700 |
Tips
SRMGe16/SRMGe18/SRMGe20/SRMGe22/SRMGe26=Fused Semi-rebond Magnesia Chrome Brick
RMGe12/RMG14=Fused Rebonded Magnesia Chrome Brick
Advantages of Magnesia Chrome Brick
Excellent Refractory Performance
Magnesia-chrome bricks have excellent refractory performance, it can withstand temperatures above 1500°C. This makes it widely used in high-temperature industrial fields such as metallurgy, steel, and cement.
Good Corrosion Resistance
As an alkali-resistant refractory material, magnesia-chrome bricks have strong corrosion resistance, especially in the cement industry, they are often used in the manufacture of high-temperature equipment such as rotary kilns, which can effectively prevent chemical corrosion and wear.
Good Thermal Shock Stability
Directly bonded magnesia-chrome bricks have good thermal shock stability, and it is not easy to crack under the condition of rapid temperature change or rapid cooling. This feature makes it widely used in high temperature kiln lining.
Strong Snti-Wear Performance
Due to its high hardness and high density, it is not easy to wear directly combined with magnesia-chrome bricks during using process, and has good anti-wear performance, which can improve the life of the equipment.
Wide Range of Application
directly bonded magnesia-chrome bricks can be applied to the lining of high-temperature melting furnaces in various industries such as steel, cement, and glass, and can be customized according to the needs of different industries.
High Safety
directly bonded magnesia-chrome brick is a kind of refractory material that meets the requirements of environmental protection, and will not cause pollution to the environment when used. In addition, it also has safety performances such as fire protection, earthquake resistance, and wind resistance.
Classification of Magnesia Chrome Bricks
Ordinary Magnesia-Chrome Bricks
Ordinary magnesia-chrome bricks (silicate-bonded magnesia-chrome bricks), which are made of chrome ore and magnesia with more impurities (SiO2 and CaO). The firing temperature is around 1550°C. The microstructure of bricks is characterized by silicate bonding between refractory grains.Directly bonded magnesia bricks are made of chrome concentrate with low impurity content and relatively pure magnesia. The structural feature of this kind of refractory brick is that the refractory grains are mostly in direct contact. Therefore, its high temperature performance, corrosion resistance and erosion resistance are better than ordinary magnesia chrome bricks.
Semi-Rebonded Magnesite-Chrome Brick
Semi-rebonded magnesite-chrome brick refers to a refractory product fired with part of fused magnesite-chrome sand as raw material. Semi-rebonded magnesite-chrome brick have low density, low porosity, high-temperature strength, thermal shock resistance is better than recombined magnesia-chrome bricks, and strong slag erosion resistance.
Direct bonded magnesia chrome brick
Directly bonded magnesia-chrome bricks are developed on the basis of ordinary magnesia-chrome bricks. There are two main characteristics of their production. One is to use relatively pure raw materials, and the other is to use higher firing temperatures.
Fused Cast Magnesite Chrome Brick
Fused cast magnesite chrome brick refers to a fused cast refractory product made of magnesite and chromite as the main raw materials. Also known as fused magnesia chromium refractory products.Fused-cast magnesia-chrome bricks have good high-temperature strength and slag resistance, but poor resistance to sudden temperature changes. It is suitable for parts with severe slag invasion, corrosion, wear and erosion, and it is better used in continuous operation furnaces.
Application of Magnesia Chrome Brick
Metallurgical Industry
Refractory magnesia-chrome bricks are used for lining and lining boards of metallurgical furnaces, converters, electric furnaces, hot blast stoves, furnaces and furnace bottoms. It can withstand the smelting process and metal corrosion at high temperature, protect the furnace structure and prolong the service life of the equipment.
Iron and Steel Smelting
Fused semi-recombined magnesia-chrome bricks are widely used in iron and steel smelting industry, such as ladles, iron faucets, pouring nozzles and other high-temperature equipment.
Cement Industry
Magnesia-chrome bricks can be used as lining and heat insulation materials for cement kilns and rotary kilns, and can withstand the erosion of alkaline gases and materials generated at high temperatures.
Chemical Industry
Magnesia-chrome bricks can be used as lining and heat insulation materials for high-temperature reactors, pipelines and hydrogenation equipment in the coal chemical industry, and have good corrosion resistance.