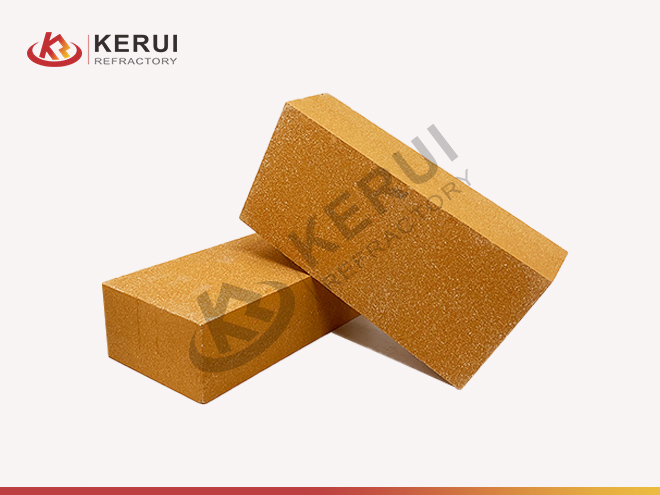
Clay Insulation Brick
- Bulk Density (g/cm³)≤: 0.5-1.5
- Thermal Conductivity (W/m·k)≤: 0.23-0.65
- Cold Crushing Strength (MPa)≥: 0.8-6
- Permanent Linear Change/%: -2-1
- Standard Size: 230*114*65mm
- Certification: ISO9001/ISO14001/ISO45001/ISO50001
- Sample: testing of sample is available
Description of Clay Insulation Brick
Clay insulation bricks and it is also called clay lightweight bricks. It is heat insulation refractory products made of refractory clay as the main raw material with an Al2O3 content of 30%-48%, the clay clinker is between 65%-85%. Clay insulation bricks are mainly used for the insulation layer of various kilns that do not directly contact the flame, and the operating environment temperature is 800℃-1200℃. Clay insulation brick is generally not in direct contact with the flame, and it is used in the heat insulation layer of the kiln. The main role of clay insulation bricks is to provide effective insulation and reduce heat transfer between the kiln and the outside air.
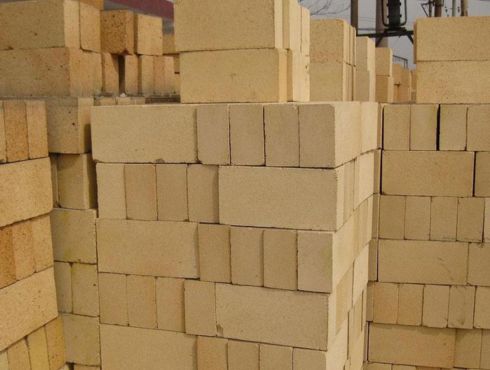
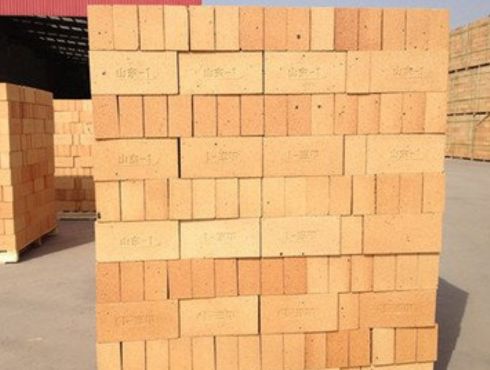
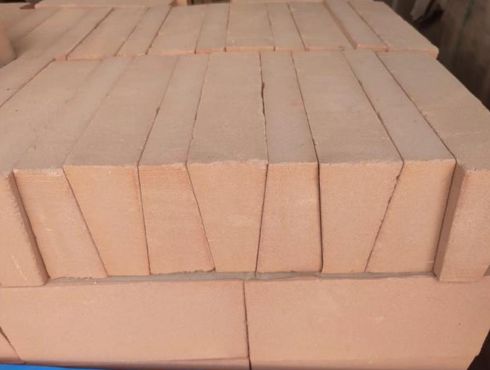
Kerui Clay Insulation Bricks Technical Data Sheet
Item/Grade | NG140-1.5 | NG135-1.3 | NG135-1.2 | NG130-1.0 | NG125-0.8 | NG120-0.6 | NG115-0.5 | ||
---|---|---|---|---|---|---|---|---|---|
Bulk Density (g/cm³) | μ0 | ≤ | 1.5 | 1.3 | 1.2 | 1.0 | 0.8 | 0.6 | 0.5 |
σ | / | 0.06 | |||||||
Cold Crushing Strength/MPa | μ0 | ≥ | 6 | 5 | 4.5 | 3.5 | 2.5 | 1.3 | 1.0 |
σ | / | 1.0 | 0.5 | ||||||
Xmin | / | 5.5 | 4.5 | 4.0 | 3.0 | 2.0 | 1.0 | 0.8 | |
Permanent Linear Change/% | Experimental Conditions | 1400℃*12h | 1350℃*12h | 1300℃*12h | 1250℃*12h | 1200℃*12h | 1150℃*12h | ||
Xmin~Xmax | -2-1 | ||||||||
Thermal Conductivity Coefficient/[W/(m·K)] ≤ Average Temperature (350±25)℃ |
Xmin | ≤ | 0.65 | 0.55 | 0.50 | 0.40 | 0.35 | 0.25 | 0.23 |
Advantages of Clay Insulation Brick
Low Thermal Conductivity
The thermal conductivity of clay insulation bricks is low, generally between 0.23-0.65 W/(m·K). This means that under the same thickness, clay insulation bricks can provide better insulation performance and reduce heat transfer.
Low Heat Capacity
The heat capacity of clay insulation bricks is generally 0.8-1.2 kJ/(kg K), this advantage means that clay insulation bricks need very little energy when washing to absorb or release heat, so they can quickly adapt to changes in temperature.
Environment Friendly
Clay insulation bricks use natural clay as raw material, which does not contain harmful substances, does not produce harmful gases and endangers human health, and is good for the environment.
Stable Performance
Clay insulation bricks have good durability and stability. Due to the good stability of the material itself, it will not cause performance degradation due to long-term high-temperature use.
Manufacturing Process of Clay Insulation Brick
Raw Material Preparation And Mixing
Clay is sieved and crushed before it can be used as raw material. First, remove the large impurities of the raw materials to obtain uniform particles, and then crush them, and then mix the treated clay and auxiliary materials (water, rice husk, etc.) by uniform stirring, so that the raw materials are fully mixed together to form a plastic shape with certain plasticity things.
Blank Making and Molding
The mixed raw materials are taken out and put into the brick making machine to make pressed bricks. By putting it into a mold for extrusion, the raw material is made into the size and shape required by the customer. Compression of adobes to give bricks a more compact density and shape.
Drying
Pressed bricks are also dried to remove moisture. Making it gradually lose moisture by drying naturally or ventilating equipment, Or gradually increasing the temperature to speed up the evaporation of moisture in the brick, but here we must pay attention to the adjustment of temperature control and ventilation to prevent the brick from cracking due to excessive drying.
Sintering
After drying is complete, it can be sintered. Usually, the brick body is calcined in a kiln at a temperature of 800℃-1100℃ and lasts for a period of time. Calcination can make the brick adobe dense and hard, and it will be over after a few hours to dozens of hours.
Cooling and Quality Inspection
After the sintering is completed, the brick body needs to be cooled, and the temperature should be lowered slowly during the cooling process. Avoid damage to the brick body caused by rapid temperature changes. After cooling, carry out quality inspection, including random inspection of appearance, size, physical performance, and other aspects of evaluation.
Application of Clay Insulation Brick
Metallurgical Industry
Clay insulation bricks can be used for the heat insulation layer of high-temperature kilns, melting furnaces, heating furnaces, etc. The low thermal conductivity and high-temperature resistance of clay insulation bricks make them an ideal choice.
Petrochemical Industry
Clay insulation bricks can be used for the thermal insulation layer of reactors, distillation towers, and other equipment. Clay insulation bricks can effectively reduce heat conduction and provide good thermal insulation performance.
Electric Power Industry
Clay lightweight bricks are mainly used in boilers, and chimneys for power plants. The Clay insulation brick is the key equipment that generates high temperatures in the process of power generation, which can improve the energy efficiency of the boiler.
Glass Industry
Clay insulation bricks are often used in the inner lining and insulation layer of glass furnaces. Clay insulation bricks can withstand high temperatures and provide good insulation, which helps to improve the energy efficiency and production efficiency of glass furnaces.