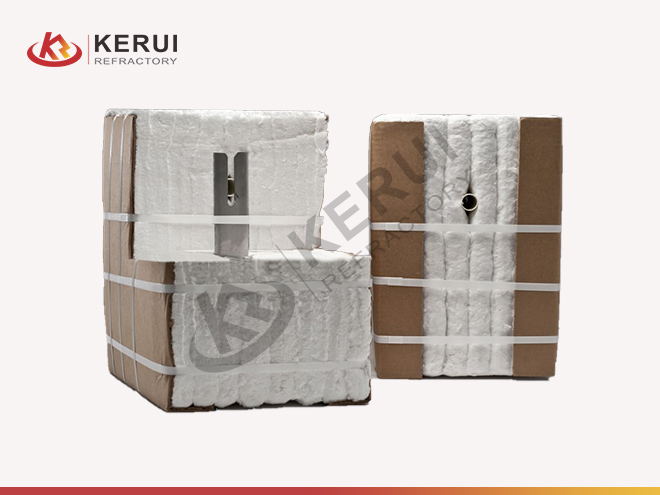
Ceramic Fiber Module
- Al2O3% (≥): 35-52
- Bulk Density (g/cm³): 160-220
- Classification Temperature (℃): 1260-1430
- Permanent Linear Change ≤/%: 2.5-3.0
- Color: White
- Certification: ISO9001/ISO14001/ISO45001/ISO50001
- Sample: testing of sample is available
Description of Ceramic Fiber Module
Ceramic fiber module is an innovative high-temperature insulation material, which combines modern technology with traditional materials to bring a new solution for high-temperature industrial applications. It uses advanced ceramic fiber technology to optimize the fiber fineness and structure to provide excellent thermal insulation performance and durability. It is made of ceramic fiber blankets that are folded or stacked and pressed into rectangular modules and employs non-exposed anchorage for economical installation and mechanical linkage.
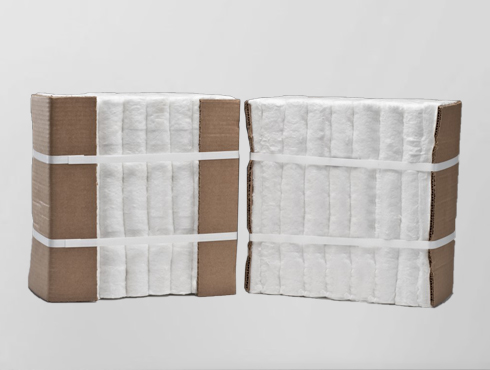
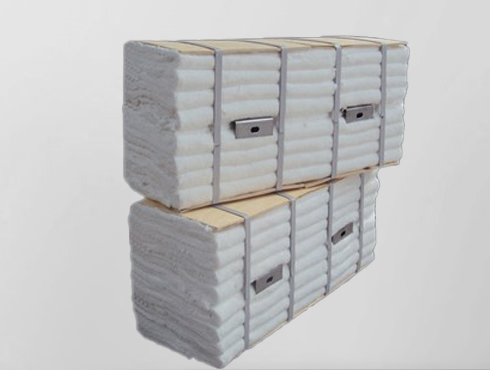
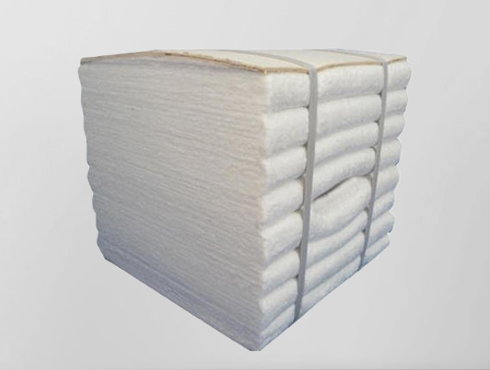
Kerui Ceramic Fiber Module Technical Data Sheet
Item/Grade | STD MODULE | HP MODULE | HA MODULE | HZ MODULE | |
---|---|---|---|---|---|
Classification Temperature/℃ | 1260 | 1260 | 1350 | 1430 | |
Chemical Composition | ω (Al2O3) ≥/% | 43 | 44 | 52 | 35 |
ω (SiO2) ≥/% | 54 | 55 | 47 | 49 | |
ω (ZrO2) ≥/% | / | / | / | 15 | |
Color | White | White | White | White | |
Bulk Density (kg/m³) | 160-220 | 160-220 | 160-220 | 160-220 | |
Permanent Linear Change ≤/% | 1000℃*24h 2.5 |
1100℃*24h 2.5 |
1200℃*24h 3.0 |
1350℃*24h 3.0 |
|
Thermal Conductivity Coefficient/[W/(m·K)] | 400℃ | 0.1 | 0.1 | 0.1 | 0.1 |
600℃ | 0.18 | 0.17 | 0.16 | 0.15 | |
800℃ | 0.2 | 0.2 | 0.2 | 0.19 | |
1000℃ | 0.27 | 0.26 | 0.26 | 0.26 |
Advantages of Ceramic Fiber Module
Low Thermal Conductivity
Due to the structure and material properties of ceramic fibers, they can effectively reduce the conduction of heat energy. Low thermal conductivity means that in high-temperature environments, ceramic fiber modules can provide better thermal insulation performance and reduce heat loss.
Shock Resistance
The flexibility and tensile strength of the ceramic fiber module help reduce the impact of the vibration structure, and its lightweight and high strength make it relatively stable in a vibrating environment.
Safety Performance
Good safety performance is mainly reflected in the characteristics of non-combustibility, low smoke toxicity, and no radioactivity. Non-combustible material means that it can resist combustion at high temperatures and the diffusion of combustion products; low smoke toxicity means that it produces less smoke and toxic gases when burning, and has less impact on human health; non-radioactive usually Refers to the ceramic fiber modules that do not produce radioactive particles or radiation.
Easy Installation
Ceramic fiber modules are flexible and malleable, allowing them to adapt to irregular or curved surfaces during installation, and it is relatively easy to remove and reinstall the modules.
Application of Ceramic Fiber Module
Petrochemical and Chemical
Ceramic fiber modules are used in petrochemical and chemical industries for heat insulation of refinery units, distillation towers, separators, incinerators, and reactors. Its application can provide high-temperature resistance, corrosion, and chemical erosion performance.
Power and Energy
Ceramic fiber modules are used in boilers and thermal power plants in the power industry, gas turbines, separators, naphtha units, and other equipment for thermal insulation and insulation materials, which can reduce energy loss and improve equipment efficiency.
Glass Manufacturing
Ceramic fiber modules are used in glass furnaces, glass fiber manufacturing equipment, and lining and insulation of glass quenching furnaces, which can withstand high temperature and chemical corrosion, and provide good thermal insulation performance and durability.
Steel Industry
Ceramic fiber modules are commonly used in heat insulation and lining materials of blast furnaces, converters, heat treatment furnaces, etc., which can ensure the stable operation of equipment and prolong the service life.
Manufacturing Process of Ceramic Fiber Module
Step 1
Raw Material Preparation: Raw materials include ceramic fiber blankets or needle-punched blankets, etc.
Step 2
Design and Cutting: design and cut the ceramic fiber blanket according to specific application requirements.
Step 3
Processing and Forming: after special processing equipment, forming under certain temperature and pressure conditions.
Step 4
Drying and Curing: The module needs to be dried at an appropriate temperature to remove moisture and volatile substances and promote the curing and stability of the material.
Step 5
Inspection and Quality Control: After the production is completed, inspection and quality control are required to ensure that it meets the specified standards.