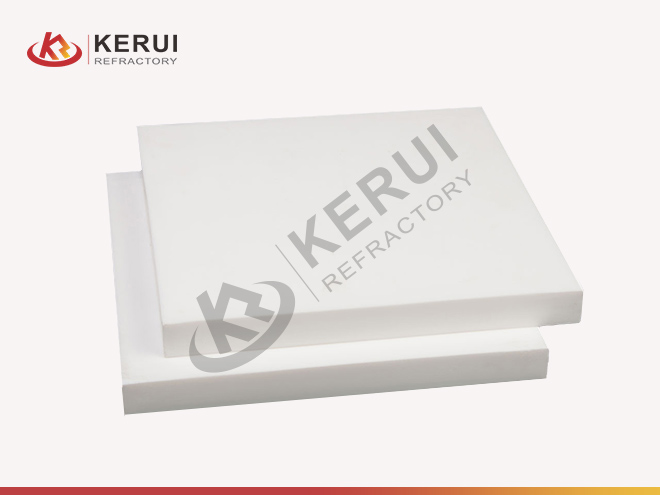
Calcium Silicate Board
- Thickness: 6-18mm
- Bulk Density (kg/m³): 230±10%
- Modules of Rupture ≥/MPa: 0.45-0.55
- Compressive Strength ≥/MPa: 0.75 -0.95
- Permanent Linear Change/%: 1000℃*16h ≤ 2.0
- Certification: ISO9001/ISO14001/ISO45001/ISO50001
- Sample: testing of sample is available
Description of Calcium Silicate Board
Calcium silicate board is a new type of lightweight multi-purpose board, which is made of silicon materials (diatomite, bentonite, quartz powder, etc.), calcium materials (slaked lime, carbide slag), reinforcing fibers (asbestos, glass fiber), etc. The calcium silicate board is made by pulping, cultivation, steaming, surface sanding, and other processes. It has a wide range of uses and can be used as non-load-bearing partition walls and ceiling boards, and can also be used to make air ducts and lining boards as well as the compartment panels and partition panels of vehicles and ships, and other places with heat insulation requirements.
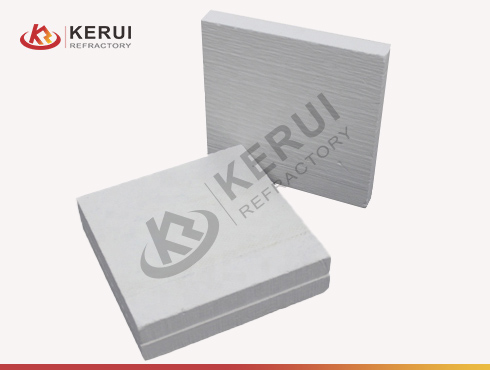
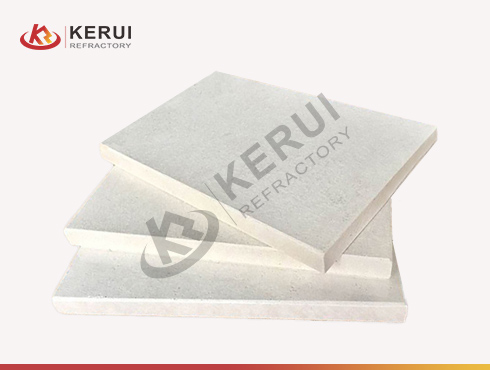
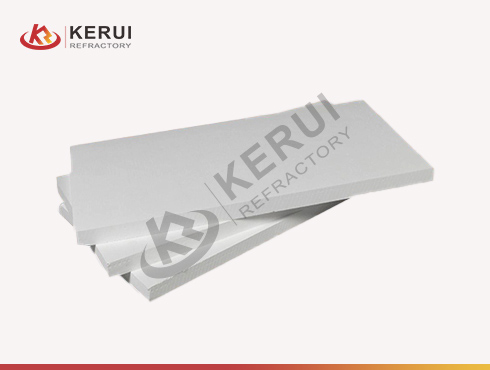
Kerui Calcium Silicate Board Technical Data Sheet
Item | Calcium Silicate Insulation Board | |||
---|---|---|---|---|
Maximum Use Temperature/℃ | 1000 | |||
Chemical Composition | ω (SiO2)/% | 46-48 | ||
ω (CaO)/% | 39-41 | |||
ω (Al2O3)/% | 0.39-0.42 | |||
ω (MgO)/% | 0.5-0.7 | |||
Color | White | |||
Bulk Density (kg/m³) | 230±10% | 250±10% | 270±10% | |
Modules of Rupture ≥/MPa | 0.45 | 0.50 | 0.55 | |
Compressive Strength ≥/MPa | 0.75 | 0.85 | 0.95 | |
Permanent Linear Change/% | 1000℃*16h ≤ 2.0 | |||
Thermal Conductivity Coefficient ≤/[W/(m·K)] | 100℃ | 0.065 | 0.067 | 0.072 |
200℃ | 0.075 | 0.077 | 0.082 | |
400℃ | 0.091 | 0.096 | 0.103 | |
600℃ | 0.132 | 0.136 | 0.138 |
CERTIFICATE OF KERUI CALCIUM SILICATE BOARD
Advantages of Calcium Silicate Board
Lightweight
Calcium silicate board is made of a light material structure with low density and weight, which makes it more convenient in the process of handling, installation, and construction, and reduces the load on the building structure.Incorporating lightweight calcium silicate boards streamlines the construction process.
Excellent Fire Performance
Calcium silicate board is an excellent fireproof material. It has a high melting point and good fire resistance, which can effectively resist the spread of flames and provide reliable protection in fires. This makes calcium silicate boards widely used in fireproof partitions, firewalls, and fireproofing devices in buildings.
Moisture Resistance
Calcium silicate board is not easy to absorb moisture and get damp, and can effectively prevent the penetration and absorption of moisture. This makes the calcium silicate board maintain stable performance when used in a humid environment and is not prone to corrosion, mildew, deformation, long service life.
Superior Heat Insulation
Calcium silicate board can prevent heat conduction and loss, reduce heat loss and provide a good heat insulation effect. This allows the calcium silicate board to play an active role in keeping the indoor temperature stable, reducing energy consumption, and improving the energy efficiency of the building.
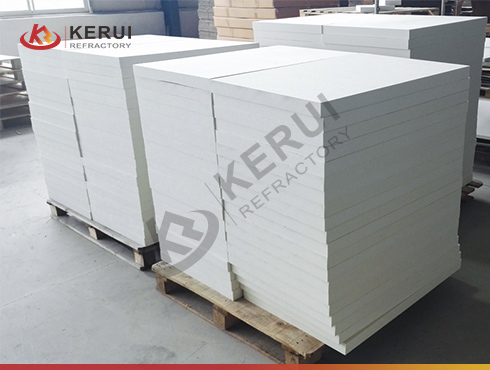
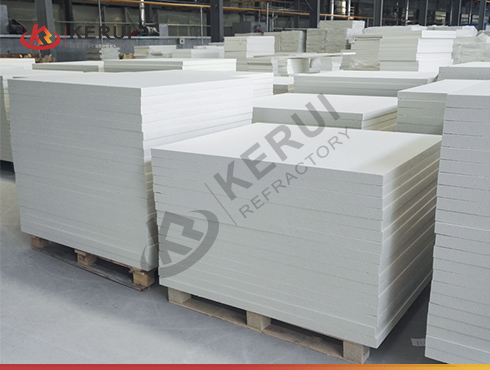
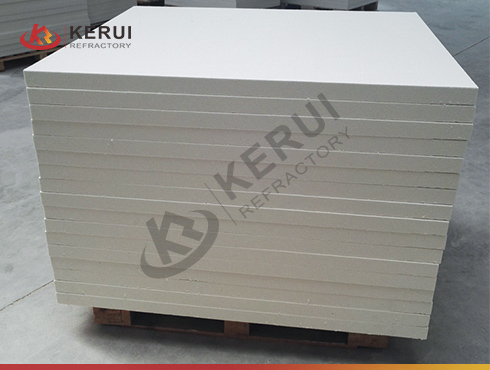
Manufacturing Process of Calcium Silicate Board
Raw Material Mix
The process involves carefully combining silica, calcium oxide, reinforcing fibers, additives, and other necessary raw materials to create a consistent and uniform slurry for the production of calcium silicate boards.
Forming
Pour the slurry into molds of the desired size and shape. Spread the slurry evenly in the mold and drain the excess water. This operation applies pressure to compact the slurry and remove trapped air.
Suppress
The formed mold is placed in a hydraulic press, applying pressure to further compact the slurry and remove excess water. The pressing process helps to achieve the density and strength required for calcium silicate boards.
Solidifying
After pressing, the boards go through a high-temperature solidifying process. The curing process promotes a chemical reaction between the ingredients to form the calcium silicate crystals that bond the boards together.
Mold Release and Cutting
After the solidifying process is complete, the boards are then cut to the desired size using a saw or other cutting device. Sand or grind at the same time for a smooth and even surface.
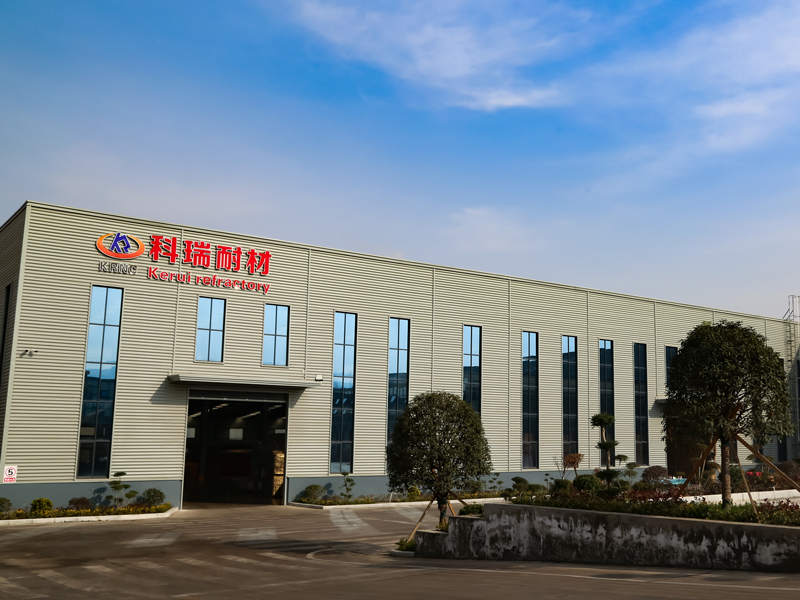
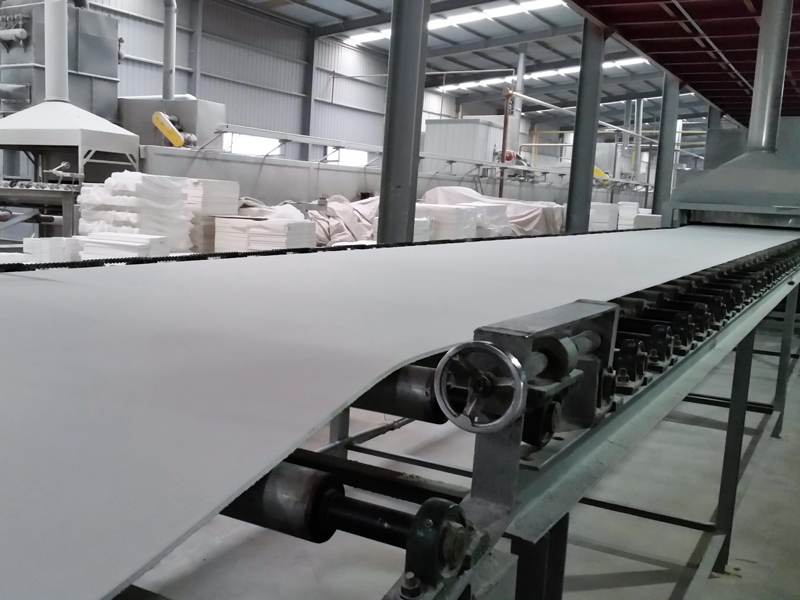
Application of Calcium Silicate Board
Furnace Lining
Calcium silicate board is widely used as a lining material for industrial furnaces. It provides insulation and protection against high temperatures, thermal shock, and chemical corrosion. It can be installed to create a lining that effectively contains heat and prevents energy loss.
Kiln and Oven Construction
Calcium silicate boards are used in the construction of kilns and ovens. Its high-temperature resistance allows it to withstand the extreme heat generated in these devices. It helps maintain an even temperature distribution, increases energy efficiency, and protects the surrounding environment from excessive heat radiation.
Heat Shields
Calcium silicate boards are used to manufacture heat shields and enclosures in various fire-resistant environments. It helps contain heat, protect surrounding structures and people, and maintain a controlled temperature environment.
Residential Building
Calcium silicate boards are commonly used in interior walls, ceilings, and floors of buildings. It provides a fire-resistant and durable surface for creating partitions and dividing spaces in buildings.
Marine Industry
Calcium silicon boards are often used in ship interiors, ship heat insulation, offshore platform installations, etc. Its heat resistance can effectively reduce changes in the internal temperature of ships and help the construction and maintenance of offshore platforms.
Medical industry
Calcium silicate board can be used in medical facilities mainly inward partitions, medical equipment heat insulation, sound insulation, acoustic control, etc. It not only meets fire resistance and durability but also reduces noise transmission and ensures patient privacy and safety.
KERUI REFRACTORY PRDUCTS PACKAGING&SHIPPING