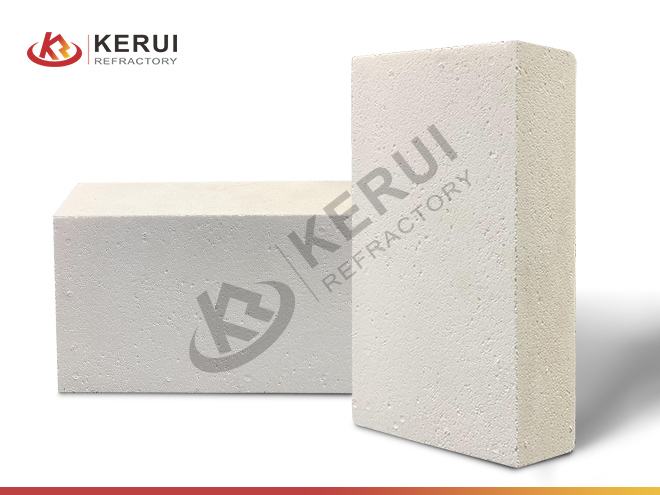
Alumina Bubble Brick
- Al2O3≥/%: 90-99
- Bulk Density (g/cm³): 1.3-1.9
- Cold Crushing Strength ≥/MPa: 6-18
- Thermal Conductivity Coefficient (1000℃)/[W/(m·K)]: 0.9-1.2
- Standard Size: 230*114*65mm & Customized Sizes
- Certification: ISO9001/ISO14001/ISO45001/ISO50001
- Sample: testing of sample is available
Description of Alumina Bubble Brick
Alumina Bubble Brick is a light-weight insulation material, which is made of alumina hollow balls and corundum powder fired at a high temperature of 1700℃. Alumina hollow bricks are composed of numerous interconnected hollow air cells, which leads to their lightweight characteristics. All the air bubbles are evenly distributed in the brick, forming a porous structure, which not only reduces the density of the brick but also maintains a high strength.
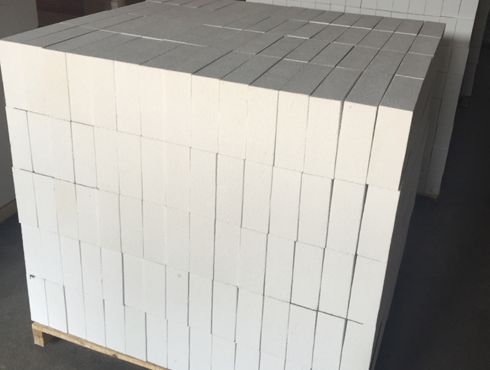
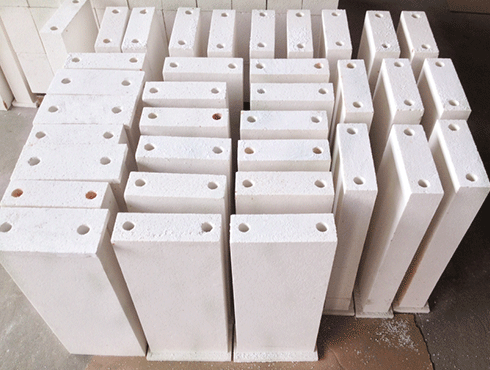
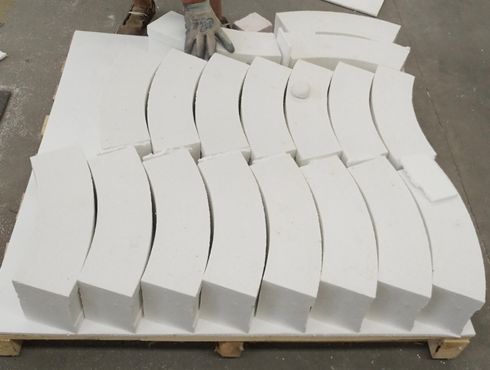
Kerui Alumina Bubble Brick Technical Data Sheet
Item/Grade | LQZ-99-1.4 | LQZ-99-1.6 | LQZ-99-1.8 | LQZ-95-1.4 | LQZ-95-1.6 | LQZ-95-1.8 | LQZ-90-1.4 | LQZ-90-1.6 | LQZ-90-1.8 |
---|---|---|---|---|---|---|---|---|---|
ω (Al2O3) ≥/% | 99 | 95 | 90 | ||||||
ω (SiO2) ≤/% | 0.3 | / | / | ||||||
ω (Fe2O3) ≤/% | 0.2 | 0.2 | 0.2 | ||||||
Bulk Density (g/cm³) | 1.3-1.5 | 1.5-1.7 | 1.7-1.9 | 1.3~1.5 | 1.5-1.7 | 1.7-1.9 | 1.3-1.5 | 1.5-1.7 | 1.7-1.9 |
Cold Crushing Strength ≥/MPa | 6 | 10 | 12 | 8 | 12 | 16 | 10 | 14 | 18 |
Thermal Conductivity Coefficient (1000℃)/[W/(m·K)] | 0.9 | 1.1 | 1.2 | 0.9 | 1.1 | 1.2 | 0.9 | 1.1 | 1.2 |
Permanent Linear Change (1600℃*3h)/% | -0.3~+0.3 | -0.3~+0.3 | -0.3~+0.3 |
Advantages of Alumina Bubble Brick
Excellent Heat Insulation Performance
The existence of hollow balls effectively blocks the conduction of heat in the material in the brick body and reduces the loss of heat. This feature makes alumina hollow bricks have an excellent effect in heat insulation.
Extremely High Heat Resistance
The refractoriness of alumina hollow bricks is above 1850℃, and the bricks can maintain the stability and integrity of the structure in medium and high-temperature environments.
Saving Energy Consumption
Using alumina hollow bricks as thermal insulation materials can reduce the energy consumption of industrial equipment. It can reduce heat loss and waste, and improve energy utilization in industrial production processes.
Environmental Friendliness
Aluminum oxide hollow bricks are made from natural aluminum oxide and other mineral components, free from harmful substances, and environmentally friendly. Their lightweight design also reduces energy consumption and resource usage during transportation and construction processes.
Manufacturing Process of Alumina Bubble Brick
Preparation and Mixing Of Raw Materials
Collecting alumina powder, foaming agent, and other auxiliary materials required for alumina hollow spheres. Mix them evenly together according to specific ratios and recipes, and then add the mixture to the mixing equipment to ensure that the individual combinations are fully integrated.
Foaming and Expansion
After adding a foaming agent to the mixture, and then chemical and physical reactions occur, the mixture will expand and bubble.
Forming
Then put the foamed mixture into the required mold, and use vibration or pressure to press it into a compact brick shape.
Drying and Curing
The formed alumina hollow bricks should be dried and cured in an appropriate environment so that can achieve a certain strength.
Sintering
The dried bricks should be sintered in a high-temperature kiln at a temperature between 1200℃ and 1800℃, and the interparticle bonding between alumina particles will occur to form the structure of the brick body.
Cooling and Packaging
After sintering, the bricks should be cooled and inspected for quality. Package and store the qualified bricks through inspection, ready for shipment or use.
Application Fields of Bubble Alumina Brick
Metallurgical Industry
Refractory lining and insulation layer of the smelting furnace;
The insulation layer and furnace wall of the high-temperature heat treatment furnace;
The Insulation layer of the casting mold;
Chemical Industry
Refractory lining for chemical reactors;
Insulation for petrochemical plants;
Insulation for high-temperature pipes and vessels;
The insulation layer of high-temperature gas separation equipment;
Power Industry
Refractory lining and insulation layer of thermal power boiler;
Gas turbine insulation and furnace walls;
Refractory structures and insulation for nuclear power plants;