Огнеупорные литейные материалы для продажи
Огнеупорные литейные материалы Kerui состоят из огнеупорного заполнителя, огнеупорного порошка, связующего и других добавок и могут использоваться непосредственно или с добавлением соответствующего количества воды или других жидкостей. После заливки или выстреливания на место литой материал затвердевает и отвердевает, образуя прочную и долговечную огнеупорную футеровку. Огнеупорные литые материалы могут быть установлены различными методами в зависимости от конкретного применения и оборудования. Например, литьем, напылением, заглаживанием и нагнетанием.
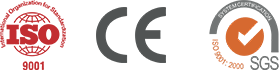
Al2O3%: 40-95
Насыпная плотность: (г/см³): 1.8-2.5
Прочность на сжатие: (МПа): 20-150
Максимальная температура эксплуатации: (℃): 1300-1800
Образец: тестирование образца доступно
Классификации огнеупорного литья KERUI
Области применения огнеупорного литья Kerui
Огнеупорный литейный материал - это специальный материал, обладающий высокой термостойкостью, коррозионной стойкостью и износостойкостью. Он может защитить оборудование от высокой температуры, коррозии и износа, обеспечивая нормальную работу производственного оборудования и безопасность персонала и имущества.
Цемент и известь, огнеупорные литейные материалы в основном используются на цементных заводах, включая теплоизоляционную футеровку; огнеупорные литейные материалы обычно используются в подогревателях вращающихся печей для обжига извести, передних и задних горловинах печей.
Огнеупорные литейные материалы в основном используются в высокотемпературных печах, таких как печи для выплавки стали, электролитические камеры для алюминия, печи для плавки стекла и т.д.
Огнеупорные литейные материалы в основном используются для футеровки различных химических реакторов и резервуаров.
Огнеупорные литейные материалы могут использоваться в футеровке электрических котлов и печей, выдерживающих горение в условиях высоких температур и давления.
-
Цемент и известь
-
Металлургическая промышленность
-
Химическая промышленность
-
Электростанция
Преимущество огнеупорных литейных материалов

Легкие заполнители и частицы в огнеупорных литейных материалах уменьшают теплопередачу и обеспечивают отличные теплоизоляционные свойства, которые снижают потери тепла и повышают энергоэффективность печей и другого оборудования для термообработки. Добро пожаловать в Kerui, мы предоставим вам продукцию лучшего качества по разумной цене.
Огнеупорные литейные материалы обычно изготавливаются с использованием высокоэффективных связующих веществ и мелкозернистых заполнителей, которые правильно смешиваются и отверждаются, образуя высокопрочную структуру. Эта высокая прочность позволяет огнеупорным материалам выдерживать механические и термические нагрузки при высоких температурах, сохраняя структурную стабильность и целостность печи.
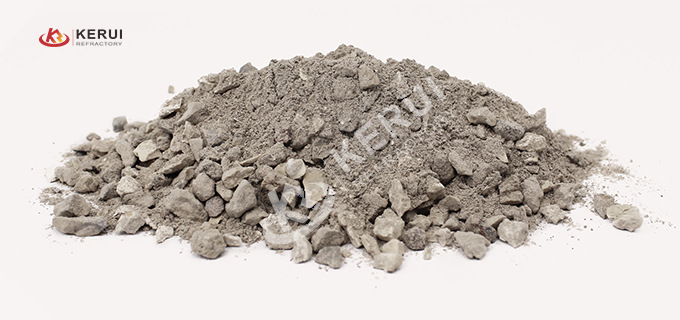

Литьевые материалы подходят для оборудования различных форм и размеров. Они могут быть адаптированы к конкретным формам и конфигурациям, их можно быстро заливать, распылять или сглаживать для удовлетворения потребностей широкого спектра оборудования и процессов, и они просты в изготовлении. Добро пожаловать на завод Kerui, мы предоставим вам лучший сервис.
Огнеупорные литые материалы могут быть изготовлены на основе заполнителей и связующих, обладающих хорошей устойчивостью к химическим воздействиям. Эти материалы устойчивы к воздействию коррозионных сред, таких как расплавленные металлы, растворы кислот и щелочей, а также агрессивные газы. Они защищают оборудование от эрозии под воздействием кислот и щелочей, коррозионных газов и расплавленных металлов. Добро пожаловать на запрос.

Процесс производства огнеупорных литейных материалов
Компания Kerui является профессиональным производителем огнеупорных материалов. Во-первых, мы располагаем передовым производственным оборудованием, технологиями, лабораториями и строгими отделами контроля качества, чтобы обеспечить высокое качество нашей продукции. Во-вторых, мы предоставляем индивидуальные услуги и разрабатываем индивидуальные решения в соответствии с потребностями клиентов. Кроме того, у нас есть профессиональные команды по предпродажному и послепродажному обслуживанию, которые могут предоставить клиентам комплексные решения, продукты и строительные решения.
Сертификаты Керуйского огнеупора
Kerui Group has a number of international certifications, such as, ISO9001/ISO14001/OHSAS18001/CE/SGS. Besides,
Kerui’s products also have many domestic certificates, the quality is very guaranteed, and they have been unanimously recognized by customers at home and abroad.
Упаковка и доставка огнеупорных изделий Kerui
The entire delivery process is tracked, and Kerui’s expert team solves specific project needs with the utmost professionalism.
If the customer’s project requires it, Kerui’s expert team will go to the customer’s country to provide face-to-face technical support.
Пример клиента Керуйского огнеупора
Помимо материкового Китая, компания Kerui Refractory экспортирует продукцию в более чем 50 стран и регионов на 5 континентах мира, включая Азию, Европу, Америку, Африку и Океанию.
Мы получили признание и высокую оценку клиентов по всему миру, и постоянно получаем повторные заказы и рекомендации от клиентов.
-
5Континенты
-
50+Континенты
-
1700+Континенты
-
4500+Континенты
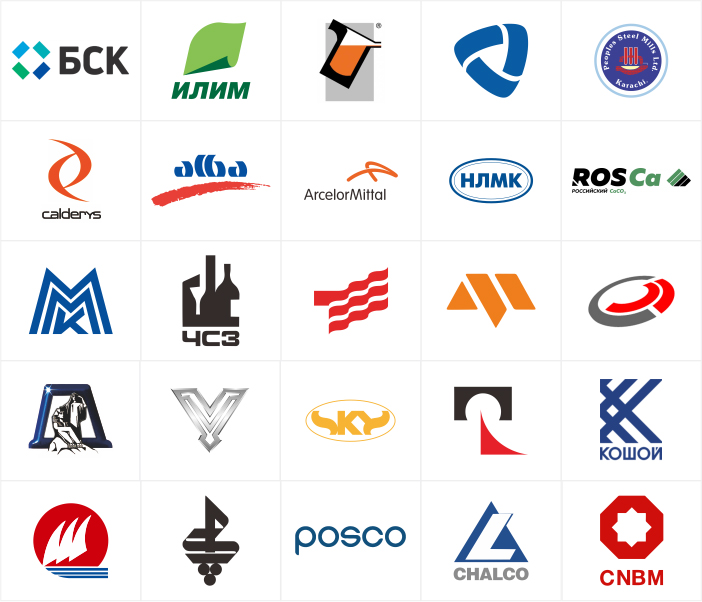
Артикул/сорт | GLJ-50 | GLJ-60 | GLJ-65 | GLJ-70 | GLJ-80 | |
---|---|---|---|---|---|---|
ω (Al2O3) ≥/% | 50 | 60 | 65 | 70 | 80 | |
Тугоплавкость ≥/℃ | 1700 | 1720 | 1720 | 1720 | 1780 | |
Насыпная плотность ≥/ (г/см³) | 110℃*24h | 2.15 | 2.30 | 2.40 | 2.45 | 2.65 |
Модуль разрыва в холодном состоянии ≥/МПа | 4.0 | 5.0 | 6.0 | 6.0 | 7.0 | |
Прочность на холодное раздавливание ≥/Мпа | 25 | 30 | 35 | 35 | 40 | |
Постоянное линейное изменение (T/℃*3h)/% | ±0.8 (1350℃) |
±0.8 (1400℃) |
±0.8 (1500℃) |
Артикул/сорт | Клей | Высокоглиноземистый | Корунд |
---|---|---|---|
ω (Al2O3) ≥/% | 45 | 75 | 92 |
ω (SiO2) ≥/% | 50 | 12 | 5 |
ω (CaO) % | 1.8 | 1.5 | 1.5 |
Насыпная плотность (г/см3) | 2.3 | 2.6 | 3 |
Прочность на холодное раздавливание/Мпа | 72 | 75 | 85 |
Постоянное линейное изменение/±% | 0.3 | 0.5 | 0.5 |
Максимальная температура эксплуатации/℃ | 1450 | 1600 | 1700 |
Необходимая вода/% | 6.0-6.5 | 6.0-6.5 | 4.0-5.0 |
Артикул/сорт | СИКАСТ 85 | СИКАСТ 80 | СИКАСТ 60 | ||
---|---|---|---|---|---|
Физические свойства | Требуемое количество (т/м3) | 2.68 | 2.6 | 2.5 | |
Вода, необходимая для литья (%) | 45084 | 45084 | 45115 | ||
CCS (кг/см2) | @ 110℃x24h | 650(140) | 500(90) | 450(70) | |
@ 1000℃x3h | 850(150) | 600(150) | 550(100) | ||
@ 1350℃x3h | 1100(250) | 1000(250) | 1000(250) | ||
PLC (%) | @ 110℃x24h | -0.06 | -0.06 | -0.06 | |
@ 1000℃x3h | -0.1 | -0.1 | -0.2 | ||
@ 1350℃x3h | -0.1 | -0.1 | -0.12 | ||
TC (ккал/мч℃) | @ 350℃ | 11.5 | 11 | 8 | |
Химические свойства | ω (Al2O3)/% | 9 | 9 | 20 | |
ω (SiC + C)/% | 83 | 78 | 58 |
Артикул/сорт | NS-1.6 | NS-1.8 | NS-2.0 |
---|---|---|---|
ω (SiO2) ≥/% | 45 | 48 | 52 |
Насыпная плотность ≥/ (г/см³) | 1.6 | 1.8 | 2.0 |
Прочность на холодное раздавливание ≥/МПа | 5 | 8 | 10 |
Кислотостойкость ≥/% | 95 | 95 | 95 |
Коэффициент теплопроводности ≤ /[Вт/(м-К)] (350±25℃) | 0.5 | 0.55 | 0.60 |
Температура эксплуатации/℃ | 800 | 900 | 1000 |
Артикул/сорт | КР-1 | КР-2 | КР-3 | |
---|---|---|---|---|
ω (Al2O3) /% | 70 | 75 | 85 | |
ω (SiO2) /% | 25 | 17 | 13 | |
ω (Fe2O3) /% | 1 | 1 | 1 | |
Насыпная плотность (г/см3) | 2.7 | 2.8 | 2.9 | |
Прочность на холодное раздавливание/МПа | 110℃*24h | 100 | 110 | 120 |
1100℃*3h | 100 | 110 | 125 | |
1400℃*3h | 115 | 120 | 15 | |
Модули разрыва в холодном состоянии/МПа | 110℃*24h | 15 | 15 | 18 |
1100℃*3h | 16 | 17 | 19 | |
1400℃*3h | 17 | 18 | 5 | |
Нормальная температура Износ/см3 | 7 | 6 | 1500 | |
0.2Mpa Тугоплавкость под нагрузкой/℃ | 1450 | 1480 | 25 | |
Максимальная температура эксплуатации/℃ | 1550 | 25 | 1600 | |
Постоянное линейное изменение/% | 1300℃*3h | -0.3 | -0.2 | -0.2 |
Артикул/сорт | F1 | F2 | F3 | |
---|---|---|---|---|
ω (Al2O3) ≥/% | 80 | 70 | 65 | |
Прочность на изгиб при комнатной температуре ≥/Мпа | 110℃*24 часа после высыхания | 12.0 | 10.0 | 9.0 |
1110℃*3 часа после высыхания | 12.0 | 10.0 | 6.5 | |
Прочность на сжатие при нормальной температуре ≥/Мп | 110℃*24 часа после высыхания | 90 | 80 | 70 |
1110℃*3 часа после высыхания | 90 | 80 | 50 | |
1110℃Прочность на изгиб после 5 циклов закалки в воде и быстрого нагрева при комнатной температуре/Мп ≥ | 5.5 | 5 | 5 | |
Постоянное линейное изменение/% | 1110℃*3 часа после сжигания | ±0.5 | ±0.5 | ±0.5 |
Артикул/сорт | GJ80 | GJ90 | GJ95 |
---|---|---|---|
ω (Al2O3) ≥/% | 80 | 90 | 95 |
Насыпная плотность ≥/ (г/см³) | 2.7 | 2.8 | 3.2 |
Прочность на изгиб ≥/МПа | 9 | 10 | 11 |
Прочность на сжатие ≥/МПа | 60 | 60 | 60 |
Постоянное линейное изменение ≤/% | ±0.5 | ±0.5 | ±0.5 |
Артикул/сорт | KRMJ-55 | KRMJ-60 | KRMJ-65 | KRMJ-70 |
---|---|---|---|---|
ω (Al2O3) ≥/% | 55 | 60 | 65 | 70 |
Насыпная плотность ≥/ (г/см³) | 2.3 | 2.4 | 2.5 | 2.6 |
Прочность на изгиб ≥/МПа | 7 | 7 | 8 | 9 |
Прочность на сжатие ≥/МПа | 40 | 50 | 60 | 70 |
Постоянное линейное изменение ≤/% | ±0.5 | ±0.5 | ±0.5 | ±0.5 |
Артикул/сорт | QJ-0.5 | QJ-0.8 | QJ-1.0 | QJ-1.1 | QJ-1.3 | QJ-1.5 | QJ-1.8 | |
---|---|---|---|---|---|---|---|---|
Насыпная плотность (г/см³) | 0.5 | 0.8 | 1.0 | 1.1 | 1.3 | 1.5 | 1.8 | |
Макс. Температура эксплуатации/℃ | 1150 | 1200 | 1250 | 1250 | 1300 | 1300 | 1350 | |
Коэффициент теплопроводности ≤/[Вт/(м-К)] | 350℃ | 0.15 | 0.25 | 0.3 | 0.4 | 0.45 | 0.6 | 0.65 |
700℃ | 0.20 | 0.30 | 0.4 | 0.45 | 0.5 | 0.7 | 0.75 | |
Прочность на холодное раздавливание ≥/МПа | 110℃*24h | 1.5 | 2.0 | 4.0 | 5.5 | 10 | 15 | 20 |
1000℃*3h | 1.5 | 2.0 | 5.5 | 6.5 | 15 | 20 | 30 | |
Постоянное линейное изменение (1000℃*3ч)/% | -1.5 | -1.0 | -1.0 | -0.5 | -0.5 | -0.5 | -0.5 |