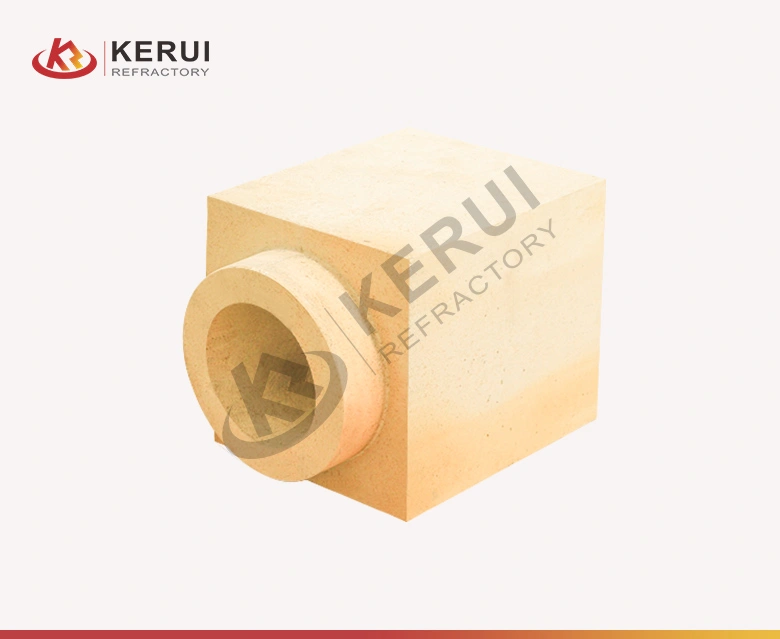
우물 블록 내화성
Well block refractory has multiple applications:
In metallurgy, it lines ladles and tundishes, protecting against molten metal’s high heat.
In cement production, it’s used in rotary kilns to resist heat and chemical corrosion.
In glass manufacturing, it safeguards melting furnaces. Its heat – resistant and durable nature makes it vital for these high – temperature industrial processes.
Description of Well Block Refractory
Refractory well blocks play a vital role in the continuous casting process in the steel industry. Made from carefully selected refractory materials, they are able to withstand extreme conditions. Well block refractory is mainly made of materials such as high – alumina, magnesia – aluminum spinel, and refractory castables. The specific refractoriness can be adjusted by changing the composition and proportion of raw materials according to different application requirements. For example, well block refractory with a higher alumina content generally has a higher refractoriness.
Technique Data of Kerui Well Block Refractory
Difference | Tundish Well Block | Ladle Well Block |
---|---|---|
위치 | Bottom of the tundish | Bottom of the ladle |
Primary Function | Controls the flow rate of molten steel into the mold and improves steel cleanliness | Controls the flow rate of molten steel from the furnace into the ladle and, in some cases, adjusts the steel composition |
Operating Stage | Continuous casting process | Steelmaking and teeming process |
Advantages of Well Block Refractory
Exceptional Heat Resistance
It can endure extremely high temperatures, often up to 1770 – 2000°C, making it suitable for use in intense heat environments like steel – making furnaces and glass melting pots.
Outstanding Chemical Stability
Resistant to chemical corrosion from various substances, whether it’s the acidic or alkaline media in industrial processes. This property ensures long – term service in chemical plants and petrochemical reactors.
높은 기계적 강도
It has sufficient strength to withstand mechanical stress, abrasion, and thermal shock. This allows it to maintain its structural integrity in equipment with frequent temperature fluctuations and mechanical impacts, such as cement rotary kilns.