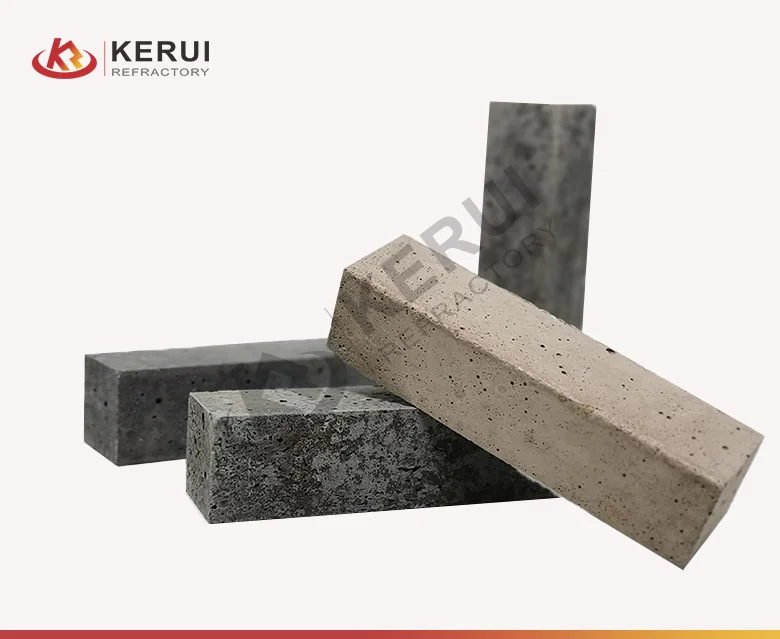
Description of Refractory Precast Shapes
Refractory Precast Shapes are essential in industries exposed to extreme heat, like steelmaking, glass production, and power generation. These components are pre – fabricated in factories using refractory materials such as high – alumina cement, fireclay, and silica.
Manufactured under strict quality control, Refractory Precast Shapes are designed to withstand temperatures up to 1,800°C or even higher. Their shapes vary from basic blocks for lining furnaces to complex structures for specialized equipment. Installation of refractory precast parts is quicker compared to traditional in – situ refractory work. This not only reduces downtime but also ensures better heat resistance and durability, thus enhancing the overall efficiency and lifespan of high – temperature industrial facilities.
Technique Data of Kerui Refractory Precast Shapes
item | 내화성 프리캐스트 모양 | ||
---|---|---|---|
GQ-92 | GQ-85 | ||
(AL2O3 + SiC)/% ≥ | 92 | 85 | |
CaO/% ≤ | 4 | 4 | |
Crushing Strength/MPa ≥ | 110℃*24h After Drying | 80 | 60 |
1100℃*3h After Reburning | 100 | 70 | |
1500℃*3h After Reburning | 120 | 100 | |
Cold Bending Strength/Mpa | 110℃*24h After Drying | 8 | 6 |
1100℃*3h After Reburning | 9 | 7 | |
1500℃*3h After Reburning | 10 | 9 | |
Heating Linear Change/% | 1100℃*3h After Reburning | ±0.5 | ±0.5 |
1500℃*3h After Reburning | ±0.5 | ±0.5 | |
벌크 밀도 | 110℃*24h After Drying | 2.9 | 2.85 |
Advantages of Refractory Precast Shapes
Exceptional Heat Resistance
Refractory Precast Shapes can endure extremely high temperatures, often exceeding 1500°C. This makes them ideal for use in furnaces, kilns, and incinerators, where they protect the underlying structures from heat damage.
High Strength and Durability
Manufactured with specialized refractory materials, these Refractory Precast Shapes maintain their structural integrity even under intense heat and mechanical stress. They resist cracking, spalling, and erosion, ensuring a long service life.
Efficient Installation
Pre – fabricated in factory – controlled environments, they come in standard or customized shapes, allowing for quick and precise installation. This reduces on – site construction time and labor costs significantly.
Good Thermal Insulation
They effectively minimize heat transfer, which helps in energy conservation and maintaining stable operating temperatures within high – temperature equipment.
Application of Refractory Precast Shapes
- Steel Industry: In steelmaking furnaces, they line the interior walls. Their high heat resistance protects the furnace shell from extreme temperatures during the smelting process, ensuring safe and continuous operation. For example, they safeguard against the 1500 – 1700°C heat of molten steel.
- Cement Production:Used in rotary kilns, refractory precast parts withstand the harsh conditions of high – temperature calcination. They prevent heat loss, improve energy efficiency, and enhance the kiln’s lifespan by resisting abrasion from moving materials.
- Power Generation: In coal – fired power plants, these components are installed in boilers. They protect the boiler structure from the intense heat of combustion, ensuring stable energy production. Their durability reduces maintenance needs and power plant downtime.