현대 산업의 고온 환경에서, 앵커 브릭는 눈에 잘 띄지 않지만 중요한 역할을 합니다. 다양한 고온 장비의 안정적인 작동을 보장하는 소리 없는 수호자 같은 존재입니다.
앵커 브릭은 안정화를 위해 사용되는 모양의 내화 벽돌입니다. 고온, 고압, 심한 진동과 같은 가혹한 조건에서 고정 및 강화 역할을 담당합니다. 독특한 구조와 특성으로 인해 수많은 산업 분야에서 없어서는 안 될 핵심 소재입니다. 재료 측면에서 앵커 브릭은 다양한 종류가 있습니다. 가장 일반적인 것은 주로 알루미노규산염 재료로 만들어진 점토 기반 앵커 브릭입니다. 알루미늄 함량이 상대적으로 낮고 내화성이 뛰어나 중온 가마 또는 보조 구역에 적합합니다. 알루미늄 함량이 48% 이상인 고알루미늄 앵커벽돌은 점토벽돌에 비해 내화성과 압축 강도가 뛰어나다는 특징이 있습니다. 시멘트 로터리 킬른의 프리 히터 또는 쿨러 섹션과 같이 고온 영역에서 중요한 역할을 합니다. 실리카를 주성분으로 하는 실리카 기반 앵커 벽돌은 내화성이 높고 압축 강도가 우수합니다. 산성 대기 부식에 대한 내성이 있어 고온 및 산성 대기가 있는 유리 가마와 같은 환경에서 뛰어난 성능을 발휘합니다.

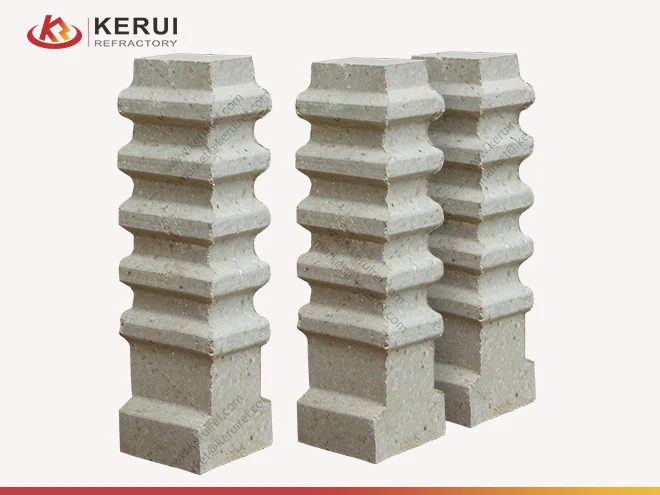

앵커 브릭은 다양한 산업 분야에서 널리 사용됩니다. 주조 산업에서는 알루미늄 합금, 스테인리스강, 니켈 기반 합금 및 티타늄 합금과 같은 고온 합금의 주조를 안정적으로 지원합니다. 야금 산업에서는 연속 주조기 결정화기, 제강 전기 아크로, 컨버터, 고온 용광로, 용광로 및 탈황 탱크와 같은 고온 장비를 라이닝하고 고정하는 데 크게 의존하고 있습니다. 또한 시멘트 산업에서는 로터리 킬른, 냉각기, 예열기 등의 장비에, 석유화학 산업에서는 정유소의 파이프라인과 저장 탱크에, 전력 산업에서는 석탄 화력 및 가스 화력 발전소의 보일러, 노, 테일 등의 장비를 고정하고 강화하는 데 사용됩니다. 고온 가마에서는 앵커 브릭이 특히 중요합니다. 내화 캐스터블 또는 내화 섬유 모듈과 같은 라이닝 재료를 고정하여 고온 및 기계적 응력 하에서 변위 또는 붕괴를 방지하여 가마 구조의 안정성과 내구성을 보장 할뿐만 아니라 기계적 수단을 통해 라이닝 재료와 가마 철판을 연결하여 가마의 전체 강도를 크게 높이고 라이닝 층의 균열 및 파손 위험을 줄입니다.
산업 기술이 지속적으로 발전함에 따라 앵커 브릭에 대한 성능 요구 사항이 증가하고 있습니다. 기업과 연구 기관은 더 나은 성능과 강력한 적용성을 갖춘 앵커 브릭을 개발하기 위해 R&D에 더 많은 투자를 하고 있습니다. 앵커 브릭은 크기는 작지만 산업용 고온 분야에서 대체할 수 없는 역할을 합니다. 전통적인 산업부터 신흥 산업에 이르기까지 어디에나 존재합니다. 앞으로 지속적인 기술 혁신과 응용 분야의 확대로 앵커 브릭은 산업 발전의 여정에서 더욱 영광스러운 장을 써서 다양한 산업의 효율적이고 안정적인 운영을 확실하게 보장 할 것입니다.